Regular inspection and maintenance of SCBAs are essential to ensuring the safety and effectiveness of the equipment. This article provides tips to help you best maintain SCBAs and perform SCBA inspections to improve fire and life safety.
By following these best practices, organizations can minimize the risk of equipment failure and keep their personnel protected in hazardous environments.
SCBA Equipment Overview
- What is a SCBA?
- SCBA stands for Self-Contained Breathing Apparatus. It is a type of personal protective equipment (PPE) used by first responders, such as firefighters and rescue workers, to provide respiratory protection in environments where there is limited or no access to oxygen.
- Physical Description:
- An SCBA typically consists of a face piece that covers the user’s mouth and nose, a cylinder that contains compressed air, and a regulator that controls the air flow to the user. The facepiece and cylinder are connected by hoses, and the regulator is attached to the cylinder.
- Function:
- SCBAs are designed to protect against hazardous substances such as smoke, toxic gasses, and chemicals that may be present in the air during an emergency situation. They provide a reliable source of breathable air for a limited period of time, allowing first responders to safely enter and operate in hazardous environments.
There are two main types of self-contained breathing apparatus (SCBA): open-circuit SCBA and closed-circuit SCBA.
- Open-circuit SCBA: This is the most common type of SCBA and it works by providing a constant flow of breathable air from a cylinder to the wearer. The used air is expelled into the environment, and fresh air is supplied from the cylinder. Open-circuit SCBA is typically used in firefighting, hazardous materials response, and other emergency situations where the air quality is compromised.
- Closed-circuit SCBA: This type of SCBA recycles the exhaled air, purifying it and returning it to the wearer. It is typically used in situations where the air quality is not compromised and the cylinder needs to last longer, such as in underground mining or during diving operations.
Both types of SCBA provide the wearer with a constant supply of breathable air and are essential for protecting firefighters and other emergency responders in hazardous environments. The choice of SCBA will depend on the specific requirements of the user, including the type of environment, the length of time the SCBA will be needed, and the available air supply.
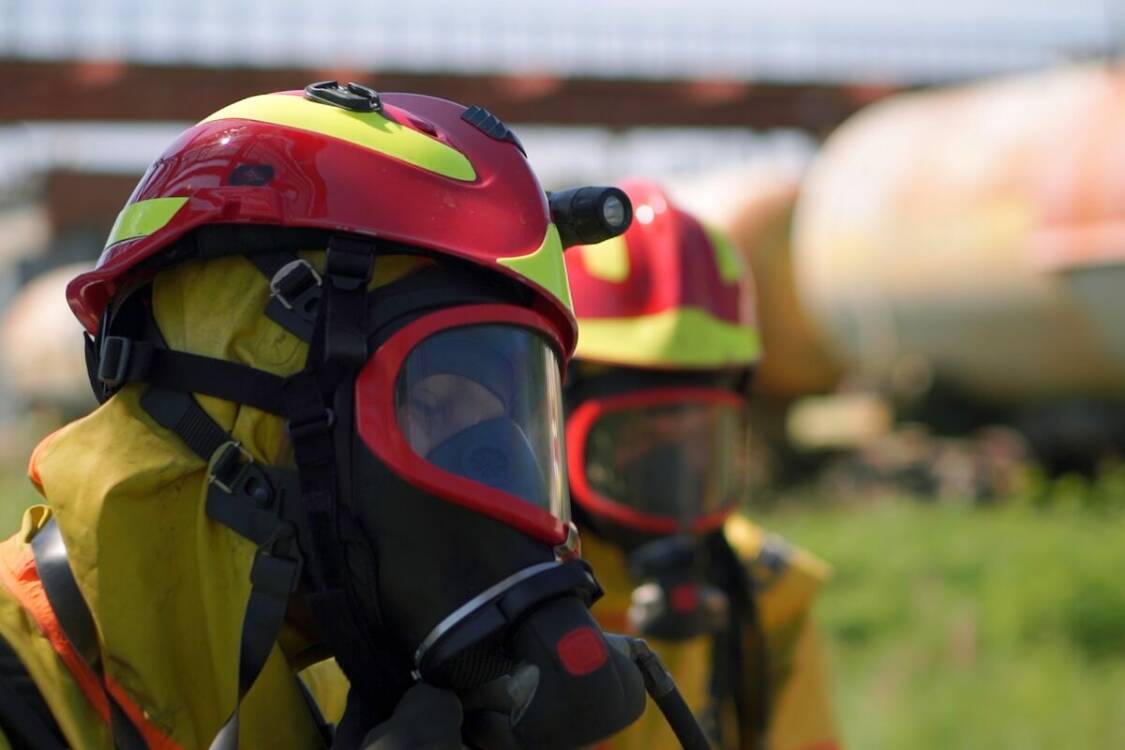
- SCBA Equipment Overview
- Industry Best Practices For Upkeep of SCBAs
- Types of SCBA Inspections and What to Know
- Tips for Performing Inspections
- Using Software for SCBA Inspections and Maintenance
- InspectNTrack Software’s Top Notch Features
- Benefits of Using Software for SCBA Inspections & Maintenance
- Invest in InspectNTrack Software
- Scan, Track, and Stay Ahead
- Conclusion
- Other Helpful Articles
- Want to learn more about InspectNTrack?
- Navigation
- Quick Links
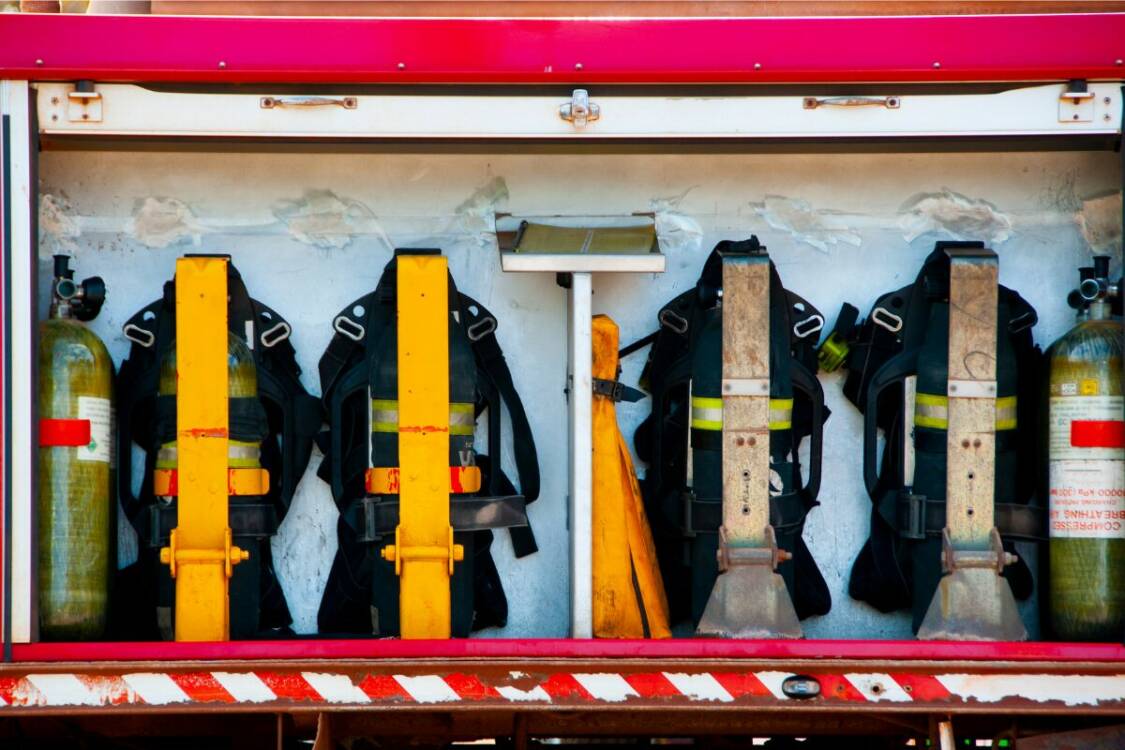
Industry Best Practices For Upkeep of SCBAs
It is common for people to have questions regarding the maintenance of SCBAs. Common questions include things such as “How often should SCBAs be inspected?” and “How are you supposed to clean SCBAs? This section addresses popular topics about SCBAs and offers insights into the best practices for their preservation.
Frequency of inspections:
As indicated by the Occupational Safety and Health Administration (OSHA), self contained breathing apparatuses should be inspected at least
- monthly,
- before each use,
- and during cleaning procedures.
This is to ensure that any issues can be quickly addressed, equipment lifespan can be prolonged, and that devices function at full capacity.
Along with the OSHA standards for inspections, NFPA 1852 advises that apparatuses which are assigned to a particular individual should be inspected daily by their owner. For apparatuses that aren’t specifically assigned, it is encouraged that they be inspected at least weekly. Though some might feel that daily or even weekly inspections are overkill, these inspections can truly be the difference between having faulty equipment in an emergency or not.
Another factor to consider for SCBA inspections is the manufacturer’s guidelines. Most SCBA manufacturers recommend that devices be inspected before and after each use. It’s also advised that SCBAs be cleaned after every use. Since SCBAs are often used by firefighters and first responders in dirty or toxic environments, it makes sense that regular cleanings are encouraged. By removing the layers of ash and soot from the exterior of the device, equipment users can much more easily assess the state of their self contained breathing apparatus.
Considering and following regulatory safety standards and manufacturer guidelines is a best practice for maintaining SCBAs.
Performing Visual and Functional Testing Inspections:
When performing SCBA inspections, it is vital to do 2 things: 1. Look over the elements of the device (visual inspections) and 2. Test to verify that all the parts are working as they should (functional testing).
Visual Inspections:
When conducting visual inspections, make sure to scan the 4 main parts of the self contained breathing apparatus for issues. These 4 main parts include the backpack and harness, air cylinder(s), regulator, and facepiece. Of course, there are other elements that make up the SCBA (straps, the airline hose, etc.), but the main 4 are the ones needing the greatest attention.
For the visual inspection of each part of the SCBA, simply look over it to make sure it is clean and free of any dust or debris. Dirt can impact the device’s ability to function properly in an emergency, and so it is essential that it be cleaned. Cleaning makes it much easier to notice issues such as tears in the backpack or cracks in the cylinders and facepiece.
Functional Testing:
Along with visual inspections, functional tests are vital for ensuring that the equipment qualifies to be used in an emergency situation. These tests don’t take long, and they can be the thing that saves someone from using faulty equipment in a dire situation.
Here are functional tests that should be performed on SCBAs.
- Air Cylinders – Verify that all cylinders are full, secure, charged and free of any leaks/damage. The pressure gauge should show at least 90% of the cylinder’s capacity. Low pressure in the cylinder could mean the difference between life and death in an emergency situation.
- Regulators – Look for signs of wear and tear on the valves/regulators. Test the regulator to confirm that it delivers air smoothly. A malfunctioning regulator could restrict airflow, making it difficult for the user to breathe safely.
- Facemask – Ensure that the facemask is safe to be worn. It shouldn’t be cracked or have any sharp edges as this can cause injury for the user. Additionally, inspect the rubber seals for any signs of wear or deterioration. A damaged seal can compromise the safety of the user by allowing contaminants into the breathing space.
- Warning device and indicators – Check to see that the EOTSI or warning device activates as it should. Ensure that the low-air alarm functions correctly, both audibly and visually.
- Buckles and Straps – Inspect the straps, harness, and buckles to ensure they are intact and function properly. Any signs of fraying, cuts, or worn-out parts should be addressed immediately. That way, the SCBA won’t fall off or become loose during a crisis.
- Verify Proper Connections: Ensure that all hoses, connectors, and fittings are securely attached. Loose or misaligned connections could lead to air leaks during use.
- Check O-rings and Gaskets: Look for cracks, tears, or other signs of wear in the O-rings and gaskets. Replace these components promptly to maintain the airtight integrity of the SCBA.
- Flow test – Perform a flow test to validate that the SCBA’s breathing machine operates according to the manufacturer’s specifications. Test the SCBA’s airflow by opening the cylinder valve and checking for any abnormal sounds or leaks.
SCBA Cleaning:
SCBAs are frequently utilized in situations involving smoke, ash, debris, and more. Because of this, they can become very dirty. In order to best see the overall condition of the self-contained breathing apparatus, users need to care for their equipment by regularly cleaning it.
The best way to go about cleaning a SCBA is to first refer to the manufacturer’s guidelines. These may offer details about specific cleaning solutions, tools, drying methods, and storage to use for SCBA upkeep. By following the manufacturer-established guidance, users can best prolong the life of the equipment. Choosing not to follow this guidance may result in void warranties, shorter life of equipment, and potential dysfunction.
When cleaning a SCBA, it is important to be very thorough. Dust and soot can easily get into cracks, making it essential for the handler to be detailed in their cleaning efforts.
Types of SCBA Inspections and What to Know
Self-contained breathing apparatuses (SCBAs) are critical to ensuring the safety of firefighters, emergency responders, and anyone working in hazardous environments where clean, breathable air is essential. Proper maintenance and inspection of SCBAs are vital to ensuring they function reliably during an emergency. Here are the inspections that users need to be familiar with and conduct on their apparatuses.
1. Daily Visual Inspections
Glance over all the parts, making sure the conditions look good. Since these inspections are so frequent, they don’t need to be super in-depth. However, they should be intentional. A brief inspection is not the same as a lazy inspection.
2. Pre-Use Inspection
Depending on how frequently the SCBA is used, a pre-use inspection may be very routine or occasional. Either way, SCBAs should be inspected before every use. This creates the opportunity to make any needed adjustments or substitutes before use should there be issues.
3. Post-Use Inspection and Cleaning
After every use, thoroughly clean and disinfect the facepiece and regulator to remove any contaminants, especially after exposure to smoke, chemicals, or biohazards. Use warm water, mild soap, and approved disinfectants for cleaning. Additionally check the air cylinder’s capacity after use and refill it according to manufacturer specifications if it is below 90%. Check for any signs of wear on the cylinder and replace it if necessary. Charge the air cylinder as needed.
4. Monthly or Periodic Inspections
At least monthly, conduct a thorough test of the entire SCBA unit, including alarms, airflow, and pressure regulators, according to the manufacturer’s guidelines. Use a test bench if available to simulate real-world use. Also, for SCBAs equipped with electronics, such as PASS devices or heads-up displays, ensure the batteries are fully charged and functional.
5. Annual Professional Servicing
At least once a year, SCBAs should undergo a full service by certified technicians. This includes a detailed inspection of every component, recalibration of pressure gauges, and thorough testing of the entire system. Certain parts may need special attention. For example, air cylinders are supposed to be tested every 3 to 5 years (depending on the material) to ensure they can withstand high pressures without failure.
Over time, even well-maintained parts can degrade. During annual servicing, wear-prone components like seals, O-rings, and harnesses should be replaced proactively to avoid failures in the field.
Tips for Performing Inspections
Regular inspections are critical to ensuring that self-contained breathing apparatuses (SCBAs) function properly and provide the protection needed in dangerous environments. Following best practices when performing SCBA inspections helps detect potential issues early and ensures the equipment is always ready for use. Here are some key steps and best practices to follow for SCBA inspections:
- Follow Manufacturer Guidelines:
- Every SCBA model may have unique inspection requirements. Always adhere to the manufacturer’s guidelines, which outline specific inspection procedures and intervals. This helps ensure the longevity of the equipment and maintains compliance with safety standards.
- Establish a Routine Inspection Schedule:
- When it comes to setting an inspection schedule for SCBAs, there are a few factors to consider: safety regulations, equipment usage, and manufacturing guidelines. Current OSHA and NFPA regulatory standards state that SCBAs should be inspected at least monthly, before each use, and during cleanings. However, SCBAs may need additional inspections and cleanings, depending on how often they are used and what the production company advises.
- Managers and equipment users should work together to outline an inspection schedule that aligns with compliance standards and that will promote effective apparatus function. This can be put into a spreadsheet, calendar, software, or other tool.
- Best practices:
- Set a schedule and stick to it.
- Inspect SCBAs at the start of every shift.
- Act promptly when issues are found or parts need replacement.
- Perform Functional Testing:
- As previously mentioned, make a point to check the 4 main components of the SCBA: the backpack and harness, air cylinder(s), regulator, and facepiece. These will be the most crucial aspects of the SCBA in a critical situation. Also look over the hoses, connections, warning indicators, O-rings, and gaskets. Finally, perform a flow test to ensure that air travels through the apparatus efficiently.
- Record and Track Inspections:
- Every SCBA unit should have an associated log where all inspections and maintenance activities are recorded. This log should include details such as the date, the individual who performed the inspection, and any issues found or corrective actions taken. Any malfunctions, damaged components, or deficiencies found during inspection should be documented and addressed immediately. If any repairs are performed, these should also be recorded, along with the date of the repair and the name of the technician. Keeping accurate records helps ensure accountability and provides a clear history of the equipment’s condition. It is also crucial for proving compliance during safety audits.
- Ensure Proper Training and Competency of Inspectors:
- It is imperative that the personnel who use and inspect SCBAs are adequately trained in both the equipment’s function and the inspection process. To keep the information fresh, regular (at least annual) refresher courses should be provided to help inspectors stay updated on current industry standards, any changes to equipment design or operation, and company policy.
- For more advanced or periodic inspections, it’s often a best practice to have certified technicians perform the tests. Certified professionals are better equipped to identify subtle issues and carry out necessary calibrations.
- Utilize Inspection Tools:
- When available, use an SCBA test bench to simulate real-world conditions and perform more detailed functional tests. This equipment can help assess how the SCBA will perform in a hazardous environment. Also, use leak detection sprays or electronic sensors to identify small leaks that might not be visible during a basic inspection. These tools can help pinpoint areas of concern before they become serious safety risks.
- Use Software for SCBA Management:
- SCBAs often have many different parts and come with a high volume of inspections. Because of this, it can be difficult to accurately document any activities, keep up with inspection schedules, and track part replacements. Software can significantly simplify these efforts. Software isn’t necessary, but it can be a great tool for saving time and energy.
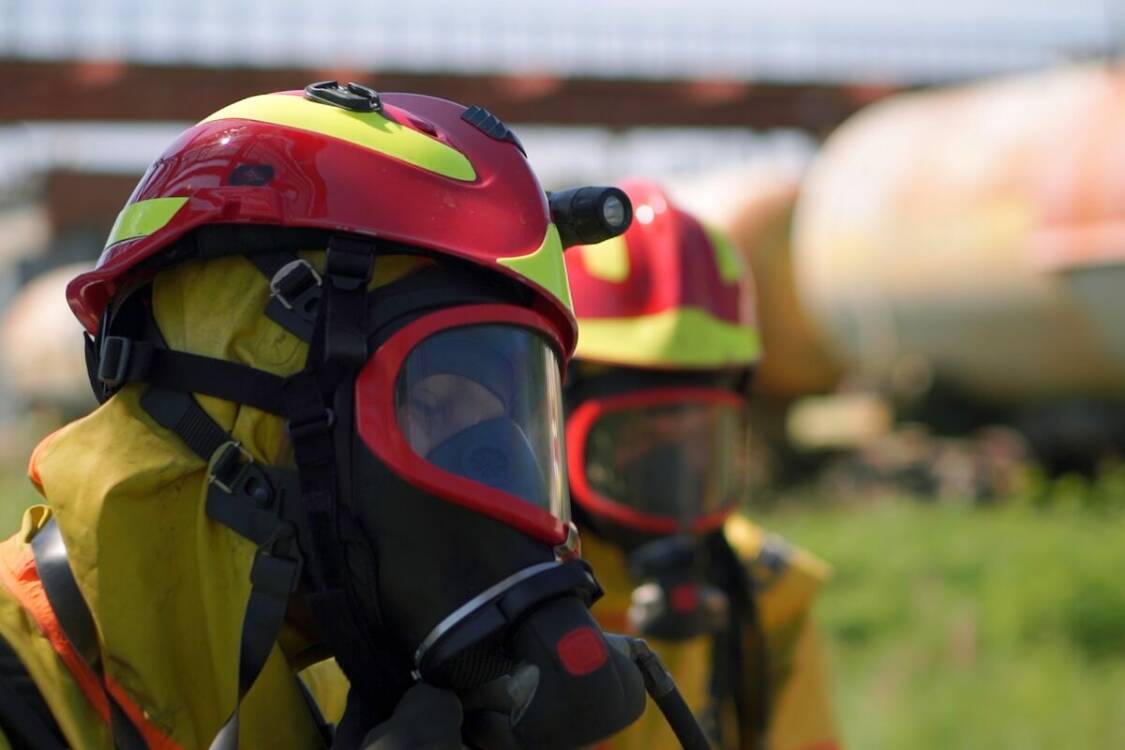
Using Software for SCBA Inspections and Maintenance
As was just mentioned, integrating software into fire safety programs is an industry best practice. The use of software can significantly decrease time needed to perform SCBA inspections and greatly improve compliance, team communication, record keeping, and much more. Because of these benefits, we want to share a little bit about our software solution and how it can aid in SCBA inspections.
InspectNTrack software is a mobile app designed with the user in mind. It is meant to simplify and streamline safety inspections, including those for self contained breathing apparatuses. The goal of integrating software into inspections and safety programs is to help refine company processes, improve compliance, increase efficiency, simplify management, and ultimately to cultivate a safer working environment.
To accomplish these goals, InspectNTrack software is equipped with a multitude of purposeful, specialized features. These features are what make InspectNTrack the best SCBA inspection app on the market. Let’s dive into the top-tier features offered in this product and how they can be advantageous for performing SCBA inspections.
InspectNTrack Software’s Top Notch Features
Here are some of the most loved InspectNTrack features for SCBA inspections and fire safety.
- Mobile App: Because there is a mobile InspectNTrack app, our software can be used on any device that runs on iOS, Windows, or Android. It works with mobile phones, desktop computers, tablets, handheld scanners and more. This means that workers can carry the technology with them on the job site, in their pocket, vest, or hand. This helps users stay up-to-date on the most recent data and remain situationally aware.
- On-the-Go Reporting: A cool feature of InspectNTrack’s software is the fact that it doesn’t need wifi to function or update. Inspections can be completed from any mobile device with no data connection required. This enables users to perform inspections and record them digitally in real time, therefore removing the hassle of papers and filling out reports manually.
- Organized Documentation: INT SCBA inspection software offers a centralized data platform, meaning that all data can be stored in a single place. This helps to keep data organized and easily retrievable in the event of an audit. Within seconds, reports can be pulled up, shared, or printed.
- User-friendly Interface: InspectNTrack is known for having a user-friendly interface, which is crucial for widespread adoption within an organization. Thanks to images, clear wording, and easily navigable pages, INT software is an intuitive tool for most users. This makes it easy for workers, supervisors, and safety professionals to access and utilize the features seamlessly.
- Dynamic Scheduling: InspectNTrack software can be used to stay up to date on both inspections and required maintenance. The system automatically schedules upcoming inspections for equipment to ensure that they are routinely completed. In fact, it can be used to track replacement dates or inspections for individual components of SCBA’s such as bottles. This feature helps remove the pain of managing various inspection schedules for different kinds of equipment, making compliance that much easier.
- Action Triggers: If there are any reported issues during SCBA inspections, the system will notify users of needed actions. These notifications encourage a prompt response to issues and help promote safety. Workers and managers alike can see what tasks need to be done and coordinate accordingly.
There are many other aspects of InspectNTrack that make it the ideal SCBA inspection app. To learn more about other features, talk to a specialist here.
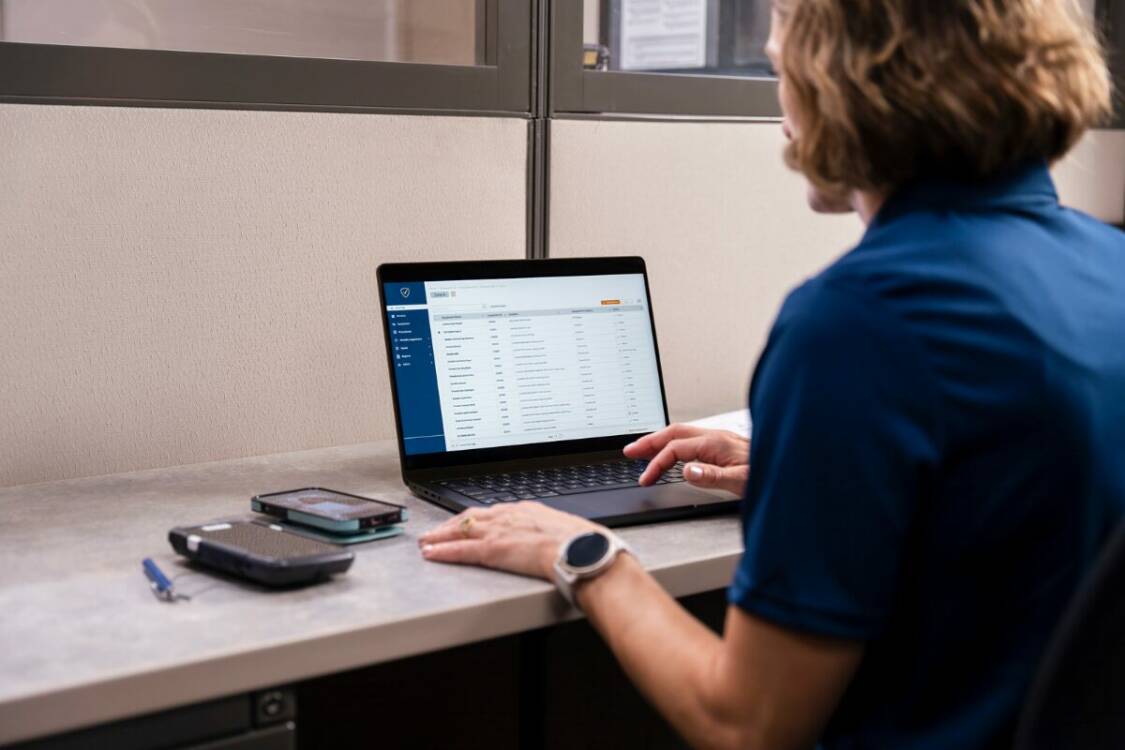
Benefits of Using Software for SCBA Inspections & Maintenance
As mentioned before, there are many reasons to conduct inspections on self contained breathing apparatuses, including ensuring that equipment functions properly, to prevent accidents, and to maximize the lifespan of equipment. However, this section will highlight the advantages of using software to perform those inspections. All of these benefits and more are available to those who use InspectNTrack’s SCBA inspection app.
- Easy Documentation and Reporting: For any program to thrive, it needs to have a sense of order. With software, you can leave behind the hassle of manual reporting and reap the benefits of a structured system. There’s no need for Excel spreadsheets, loose papers, or calendars for inspection scheduling. This makes it much easier to record inspections as they occur, keep the data organized, and retrieve information when necessary.
- Improved Transparency: Transparency is a key component of any robust safety inspection program. By utilizing InspectNTrack software, inspectors can generate detailed, timestamped digital reports that include photographs, notes, and any identified issues. Since the software automatically updates without wifi, team members can access this data in real time. This transparency fosters trust among stakeholders and ensures that necessary actions are taken promptly to address safety concerns.
- Increased efficiency: Efficiency is a high priority for virtually all companies and organizations. Thankfully, software is changing the game when it comes to efficiency. Automation and digitization help to significantly streamline the inspection process. Instead of relying solely on manual checks, inspectors can use software to schedule inspections, access digital checklists, and more. With InspectNTrack’s SCBAinspection app, it is quicker and easier than ever before to perform inspections.
- Greater Accuracy: Accuracy is another crucial aspect of cultivating a safe workplace. One of the biggest ways that INT software fosters greater accuracy in reporting is the fact that it is all digital. This helps to reduce human error, because there aren’t any misplaced or lost documents. All system data and history is stored in a centralized platform, therefore reducing the risk of lost information.
- Simplified Compliance: Thorough reporting and documentation are needed for companies and organizations to be able to prove their compliance during audits. InspectNTrack’s SCBA inspection app simplifies compliance by providing automated scheduling of inspections (which can be specified for the individual parts of SCBAs) and action triggers for identified issues that need attention. These features help managers ensure that an inspection schedule is kept up with and that problems are addressed, making OSHA compliance that much easier.
Invest in InspectNTrack Software
Want to learn more about what InspectNTrack is and how it can help with fire and life safety inspections? If so, connect with our team by requesting a demo! Our team of specialists are happy to set up a meeting to help you determine if INT software is right for your company’s needs. We believe in the power of our product to change the way safety is approached in the workplace and want to answer any questions you have. You may have come looking for valve inspection software, but InspectNTrack can do a whole lot more than that. We have a multitude of solution offerings, and hope that you will give us the chance to show just what InspectNTrack can do!
Conclusion
Self-contained breathing apparatuses are incredible tools for safety in hazardous environments. In order to maintain peak function, these devices require consistent care through SCBA inspections and maintenance. Some of the best practices for equipment care include having a schedule for SCBA inspections, performing functional and visual tests on them, and completing thorough cleanings. Other best practices include understanding the different kinds of inspections, being familiar with regulatory standards, properly training personnel, following manufacturer guidelines, and using software for program management. InspectNTrack offers a top-tier SCBA inspection software with a variety of features that can be beneficial for the upkeep of these devices. By adhering to these best practices, organizations can significantly reduce the risk of SCBA failure in critical situations. Regular inspections performed with attention to detail, proper training, and appropriate tools ensure that SCBAs remain safe, reliable, and ready to protect personnel in dangerous environments.