SCBA Inspection and Maintenance Programs
If you are charged with managing SCBA inspections and keeping the equipment in compliance with NFPA standards you might be looking for an efficient program to follow. Because SCBAs are so vital to life or death during a fire, it is important to be accurate when developing an SCBA inspection program. Software such as InspectNTrack offers plug & play SCBA inspection programs. Read on to learn more.
What Is a SCBA?
SCBA stands for Self-Contained Breathing Apparatus. It is a type of personal protective equipment (PPE) used by first responders, such as firefighters and rescue workers, to provide respiratory protection in environments where there is limited or no access to oxygen.
An SCBA typically consists of a face piece that covers the user’s mouth and nose, a cylinder that contains compressed air, and a regulator that controls the air flow to the user. The face piece and cylinder are connected by hoses, and the regulator is attached to the cylinder.
SCBAs are designed to protect against hazardous substances such as smoke, toxic gases, and chemicals that may be present in the air during an emergency situation. They provide a reliable source of breathable air for a limited period of time, allowing first responders to safely enter and operate in hazardous environments.
There are two main types of self-contained breathing apparatus (SCBA): open-circuit SCBA and closed-circuit SCBA.
- Open-circuit SCBA: This is the most common type of SCBA and it works by providing a constant flow of breathable air from a cylinder to the wearer. The used air is expelled into the environment, and fresh air is supplied from the cylinder. Open-circuit SCBA is typically used in firefighting, hazardous materials response, and other emergency situations where the air quality is compromised.
- Closed-circuit SCBA: This type of SCBA recycles the exhaled air, purifying it and returning it to the wearer. It is typically used in situations where the air quality is not compromised and the cylinder needs to last longer, such as in underground mining or during diving operations.
Both types of SCBA provide the wearer with a constant supply of breathable air and are essential for protecting firefighters and other emergency responders in hazardous environments. The choice of SCBA will depend on the specific requirements of the user, including the type of environment, the length of time the SCBA will be needed, and the available air supply.
Inspection App Solutions
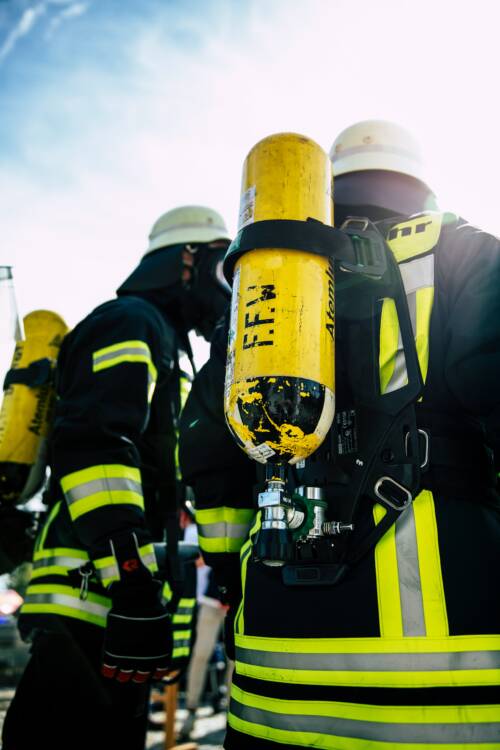
What Types of Companies Need To Have SCBAs?
SCBAs are typically used by a variety of companies and organizations that need to provide respiratory protection for their employees in hazardous environments, including:
- Fire departments: Firefighters use SCBAs to protect themselves from toxic fumes, smoke, and heat while fighting fires.
- Industrial plants: Workers in chemical, petrochemical, and other industrial plants may use SCBAs when working with hazardous chemicals and gases.
- Emergency response teams: Emergency response teams, such as hazardous materials (HAZMAT) teams, use SCBAs when responding to incidents involving hazardous substances.
- Construction companies: Construction workers may use SCBAs when working in environments with poor air quality or limited ventilation, such as in underground tunnels or trenches.
- Military: Military personnel may use SCBAs in combat or during training exercises in contaminated environments.
- Mining companies: Miners may use SCBAs when working in underground mines with poor air quality.
- Oil and gas companies: Workers in the oil and gas industry may use SCBAs when working in offshore drilling platforms or when responding to spills and leaks.
In general, any company or organization that operates in hazardous environments where there may be limited or no access to breathable air may use SCBAs to provide respiratory protection for their employees. Companies that use SCBAs need to understand how they work and perform regular SCBA inspections. These steps help ensure that the wearer is properly protected.
How Does a SCBA Work?
A SCBA works by providing the user with a supply of clean, breathable air from a cylinder of compressed air that is carried on their back. The air is regulated by a valve and delivered to the user through a face piece that covers their mouth and nose.
Here’s how the SCBA works in more detail:
- Compressed air is stored in a cylinder: The cylinder is filled with compressed air to a high pressure, typically around 4,500 psi.
- Air is regulated by a valve: The valve controls the flow of air from the cylinder and reduces the pressure to a level that is safe for breathing.
- Air is delivered through a face piece: The air is delivered to the user through a facepiece that covers their mouth and nose. The face piece seals tightly to the face, creating a positive pressure inside the mask to prevent contaminated air from entering.
- Air is breathed in by the user: The user breathes in the clean, regulated air through the facepiece, providing them with a reliable source of breathable air in an environment where the air may be contaminated or lacking in oxygen.
- Exhaled air is expelled: The user exhales through a valve in the facepiece, and the exhaled air is expelled out of the mask and into the environment.
SCBAs also typically include alarms and gauges to alert the user to low air levels or other critical information, as well as straps and harnesses to secure the cylinder and face piece to the user’s back. The combination of a reliable source of breathable air, a tight-fitting face piece, and alarms and gauges help ensure the user’s safety and allow them to operate effectively in hazardous environments.
SCBA Regulations
SCBAs are regulated by several agencies, both at the national and international level, to ensure that they are safe and effective for use in hazardous environments. Some of the key regulations that apply to SCBAs include:
- OSHA: In the United States, SCBAs are regulated by the Occupational Safety and Health Administration (OSHA) under 29 CFR 1910.134, the Respiratory Protection standard. This standard specifies the requirements for selecting, using, and maintaining respiratory protective equipment, including SCBAs.
- NIOSH: The National Institute for Occupational Safety and Health (NIOSH) is the federal agency responsible for certifying SCBAs in the United States. NIOSH evaluates SCBAs to ensure that they meet specific performance standards, including minimum levels of protection, breathability, and durability.
- CEN: In Europe, SCBAs are regulated by the European Committee for Standardization (CEN), which establishes performance standards for personal protective equipment, including SCBAs.
- NFPA: The National Fire Protection Association (NFPA) also sets standards for SCBAs used by firefighters in the United States. NFPA 1981, Standard on Open-Circuit Self-Contained Breathing Apparatus (SCBA) for Emergency Services, establishes performance requirements for SCBAs used by firefighters.
These regulations help to ensure that SCBAs are effective and safe for use in hazardous environments, and they provide a minimum level of protection for workers who use these devices. Companies that use SCBAs are responsible for ensuring that they comply with these regulations and that they are properly used and maintained to ensure their effectiveness.
SCBA Inspection Requirements
SCBAs require regular inspection and maintenance to ensure their effectiveness and to prolong their lifespan. The specific inspection and maintenance requirements for SCBAs will depend on the manufacturer’s recommendations, as well as any relevant regulations, such as OSHA or NFPA standards. However, some general inspection and maintenance requirements for SCBAs include:
- Visual inspections: Before each use, the user should perform a visual inspection of the SCBA to ensure that it is free of damage and in good working order. This includes checking the cylinder, valve, regulator, facepiece, harness, and other components for signs of damage, wear, or corrosion.
- Hydrostatic testing: Cylinders must be hydrostatically tested at regular intervals to ensure their integrity and to detect any leaks or cracks. The frequency of hydrostatic testing will depend on the manufacturer’s recommendations and any relevant regulations.
- Regulator maintenance: The regulator should be inspected and maintained regularly to ensure that it is functioning properly and providing a constant air flow. This may include cleaning, lubrication, and replacement of worn or damaged components.
- Face piece maintenance: The face piece should be cleaned and disinfected regularly, and it should be inspected for signs of damage or wear. Any cracks, holes, or other defects in the face piece can compromise its protective ability.
- Alarm testing: The low air alarm and other warning devices should be tested regularly to ensure that they are functioning properly.
- Record keeping: Records of inspections, tests, and maintenance should be kept to demonstrate that the SCBA has been properly maintained and is in good working order.
It is important to follow the manufacturer’s recommendations and any relevant regulations for the inspection and maintenance of SCBAs to ensure their effectiveness and to prolong their lifespan. Regular inspection and maintenance can also help to identify and address any potential problems with the SCBA before they become serious, ensuring that the user is protected in hazardous environments.
NFPA Standards for SCBA Inspections
The National Fire Protection Association (NFPA) sets standards for firefighting equipment, including self-contained breathing apparatus (SCBAs). The NFPA standard for SCBAs used by firefighters is NFPA 1981, Standard on Open-Circuit Self-Contained Breathing Apparatus (SCBA) for Emergency Services.
This standard establishes performance requirements for SCBAs, including:
- Protection: The SCBA must provide a minimum level of protection for the user, as specified by the standard. This includes protection against toxic fumes, smoke, and heat.
- Breathability: The SCBA must provide an adequate supply of breathable air for the user, as specified by the standard. This includes a minimum air flow rate, a maximum breathing resistance, and a minimum air supply duration.
- Durability: The SCBA must be durable and withstand the rigors of firefighting, as specified by the standard. This includes resistance to impact, abrasion, and exposure to heat and chemicals.
- User comfort: The SCBA must be designed for user comfort, as specified by the standard. This includes an adjustable harness, a comfortable face piece, and an ergonomic design.
- Alarms and warning devices: The SCBA must have alarms and warning devices to alert the user to low air supply, as specified by the standard.
- Maintenance and inspection: The SCBA must be designed for easy maintenance and inspection, as specified by the standard. This includes easy access to components for inspection and maintenance, and clear instructions for maintenance and inspection procedures.
The NFPA 1981 standard helps to ensure that SCBAs used by firefighters are effective and safe for use in hazardous environments. Companies that use SCBAs must ensure that their equipment meets the requirements of the standard, and they must perform regular inspections and maintenance to ensure that the SCBAs remain in good working order.
How Often Does an SCBA Need To Be Inspected?
The frequency of inspection for self-contained breathing apparatus (SCBA) is specified by the National Fire Protection Association (NFPA) 1981 standard, which is widely recognized as the industry standard for SCBA. According to NFPA 1981, SCBA must be inspected at least annually, or more frequently if specified by the manufacturer or as required by the user’s respiratory protection program.
In addition to the annual inspection, SCBA should be inspected before and after each use, and after any maintenance or repair work. This will ensure that the SCBA is in good working condition and that any potential issues are identified and addressed in a timely manner.
It is important to remember that SCBA is a critical piece of personal protective equipment for firefighters and other emergency responders, and that regular inspections are essential to ensure its reliability and effectiveness in hazardous environments.
How To Perform an SCBA Inspection In Accordance With NFPA 1981
The National Fire Protection Association (NFPA) 1981 standard provides guidelines for the inspection, maintenance, and testing of self-contained breathing apparatus (SCBA) used by firefighters and other emergency responders. Here are the steps for performing a SCBA inspection in accordance with NFPA 1981:
- Verify the manufacturer’s information: Ensure that the SCBA meets the requirements of NFPA 1981 and check the manufacturer’s information to determine the recommended inspection interval.
- Visual inspection: Check the SCBA for any signs of damage or wear, including cracks, holes, or signs of corrosion. Check the regulator, face piece, and head harness for any damage. Check the cylinder for any signs of damage or corrosion.
- Harness and headgear: Check the headgear for proper fit, security, and damage. Ensure that the straps are secure and in good condition. Check the head harness for any damage or signs of wear.
- Regulator: Check the regulator for proper operation and that it provides a constant flow of air. Ensure that the regulator is secure and in good condition.
- Face piece: Check the face piece for proper fit, damage, and that it seals securely. Check the face piece lens for cracks or damage.
- Cylinder: Check the cylinder for proper markings, including the date of manufacture, test date, and hydrostatic test date. Check the cylinder valve for proper operation and that it is secure.
- Hose and connections: Check the breathing hose for damage or signs of wear. Ensure that the connections are secure and free of damage.
- Alarms and indicators: Check the low-air alarms, full-face pressure-demand regulators, and any other indicators for proper operation.
- Record Keeping: Document the results of the inspection and any repairs or maintenance performed. This documentation can be kept electronically with InspectNTrack software.
It is important to follow these steps carefully to ensure that the SCBA is in good working condition and that it will provide the necessary protection in the event of an emergency.
InspectNTrack’s SCBA Inspection Software
InspectNTrack’s software is designed to aid in the inspections, maintenance, and documentation for all kinds of fire and life safety equipment, including SCBAs. Our software provides users with a multitude of tools such as automated inspection scheduling, on-the-go reporting, and action triggers to ensure that inspections occur on time, actions are accurately reported, and any issues are addressed. In fact, the software app includes pre-drafted NFPA 81 inspection forms that can be used when performing SCBA inspections. This way, you can stay organized, promote safety, and maintain compliance.
Conclusion
A Self-Contained Breathing Apparatus (SCBA) is a form of personal protective equipment that provides clean air to users. It is often used in industries where respiratory protection is needed in hazardous environments. Industries that use SCBAs such as fire departments, mining companies, EMTs, and more should stay up to date on current regulations regarding the use and maintenance of SCBAs. Familiarity with these regulations, particularly NFPA 1981, will help ensure that SCBA inspections are performed properly. To simplify SCBA inspections, InspectNTrack software offers pre-drafted NFPA 1981 inspection forms for SCBA inspections. InspectNTrack makes it easy to get started with SCBA inspections today. To learn more about how InspectNTrack can help with your SCBA inspections, request a free demo!