As stated by the American Fire Sprinkler Association, “Fire sprinklers are widely recognized as the single most effective method for fighting the spread of fires in their early stages”. This means that fire sprinkler systems can make a significant difference in the event of a fire emergency. Because they are responsible for providing a rapid response to potential fire emergencies, it is a high priority to keep them in mint condition. One way to maintain optimal functionality of fire sprinkler systems is to perform regular inspections. In this article, we will guide you through the step-by-step process of inspecting a fire sprinkler system to maintain its reliability and effectiveness.
The Importance of Fire Sprinkler Inspections
Fire sprinkler systems are designed to suppress or extinguish fires, safeguarding lives and property. Because of this, they are invaluable tools for safety. Here are some stats that showcase the importance of fire sprinklers and why their inspections are so vital:
The Home Fire Sprinkler Coalition has shared that the “average fire loss in a house with a sprinkler system is $2,166 as opposed to $45,019 in a home without the protection.” Additionally, they share that fire sprinkler systems can “reduce fire damage by up to 97 percent”! And while these statistics are specifically about homes, one can reason that similar results are true of sprinklers in enterprise buildings.
These numbers help highlight the good that fire sprinkler systems can do and why keeping them in good condition is so vital. With regular inspections, it’s easy to ensure that fire sprinkler systems are compliant with regulatory requirements and capable of being used in an emergency. In this way, inspections contribute to the overall safety and functionality of the fire suppression system.
Regulations Regarding Fire Sprinkler Systems
The purpose behind fire sprinkler system inspections is to ensure that the system is functioning properly and that it is compliant with current safety regulations. Because of this, it is important that inspectors be familiar with the established standards related to fire sprinklers.
Those performing fire sprinkler system inspections should be familiar with NFPA 25, an established code from the National Fire Protection Association that outlines inspections, testing and maintenance of water-based fire protection systems.
Adhering to NFPA 25 standards is essential for the proper inspection of fire sprinkler systems. Regular inspections, testing, and maintenance are crucial to ensure the reliability and effectiveness of the system in the event of a fire. Building owners, facility managers, and those responsible for fire safety should stay informed about the NFPA requirements and work with qualified professionals to conduct thorough inspections.
There are other safety standards related to fire sprinklers, such as NFPA 13; however, NFPA 25 is the one to focus on when conducting a system inspection. For more information about fire safety and the contents of these standards, see the NFPA website.
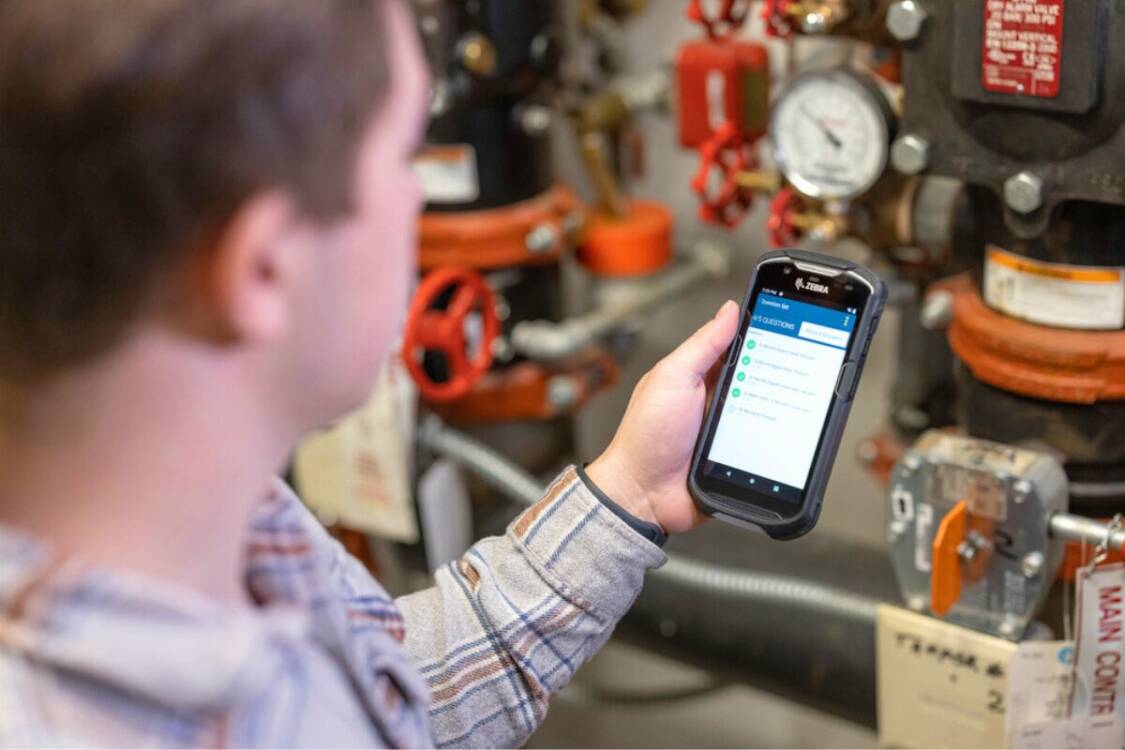
Wet vs. Dry Fire Sprinkler Systems
Before starting an inspection, it is important to understand what kind of equipment you are working with. In the case of fire sprinkler systems, there are 2 main kinds: wet and dry systems. Here is a brief overview of the two systems and their different purposes:
Wet and dry fire sprinkler systems differ primarily in their method of operation and the type of environment in which they are used. A wet sprinkler system maintains water within the pipes at all times, allowing for immediate discharge when a sprinkler head is activated by heat. This type is ideal for environments that are consistently heated and where pipes are not at risk of freezing. Conversely, a dry sprinkler system keeps the pipes filled with pressurized air or nitrogen, with water held back by a control valve. When a sprinkler head activates, the air pressure drops, allowing the valve to release water into the pipes and out through the sprinkler heads. Dry systems are typically used in areas subject to freezing temperatures, preventing water from freezing within the pipes and ensuring reliable operation in cold conditions.
Steps To Inspect a Fire Sprinkler System
Here’s a comprehensive guide on how to conduct a thorough fire sprinkler system inspection:
1. Know the Regulatory Landscape:
Before starting an inspection, become familiar with local, state, and national regulations governing fire sprinkler systems. This step is important, because there can be fines, violations, and other consequences for noncompliance with government issued regulations. As stated previously, inspectors in the United States should be familiar with NFPA 25. On top of learning about NFPA 25, also make sure you understand the inspection frequency, standards, and compliance requirements applicable to your jurisdiction.
2. Gather Necessary Tools:
Next, collect the tools needed for a detailed inspection. Ensure you have a ladder, flashlight, inspection mirror, and any specialized tools recommended by the sprinkler manufacturer or regulatory guidelines. If you’re working with overhead obstructions when checking fire sprinkler systems, hardhats, safety glasses, and gloves should be worn. For checking higher level components, make sure that proper safety procedures for ladders are adhered to.
Gathering and utilizing these tools during the fire sprinkler inspections will help prevent any injury or accident from occurring.
3. Review Documentation:
Then, examine the documentation related to the fire sprinkler system. This may include design plans, installation records, and maintenance logs. Understanding the system’s layout and history will provide you with valuable context for the inspection. As part of the documentation review, check to ensure that the owner has inspection records that indicate their conformity and compliance with NFPA 25.
4. Conduct a Visual Inspection:
Perform a visual inspection of each sprinkler head. Look for the following:
- Positioning: Ensure correct positioning without obstructions.
- Tamper Seals: Check for intact tamper seals, indicating the system’s integrity.
- Cleanliness: Verify that sprinkler heads are free from dust and debris.
- Backups: When looking at the riser, ensure there are extra sprinkler heads available for that system.
- Adequate volume: Within the rooms, look for sufficient sprinkler heads for the room’s max occupancy.
5. Verify Clearances
As part of the visual inspection, confirm there is adequate clearance around each sprinkler head. Per NFPA 25, all objects near fire sprinkler heads should be at least 18 inches from the deflector (small metal part at the sprinkler’s forward edge). Objects too close can impede water spray patterns and compromise system effectiveness. Therefore, any objects that breach the 18 inch boundary from the sprinkler head need to be moved. Though this may seem like an unnecessary step, it is an essential part of ensuring that the fire sprinkler system is able to perform its best in the event of an emergency.
6. Inspect Piping:
Next, examine the piping connecting the fire sprinkler system for signs of corrosion, leaks, or damage. Since pipes are responsible for storing the water that is then used by the sprinklers, keeping them in pristine condition will promote proper functionality of the fire sprinklers. While inspecting the piping, ensure that the piping has sufficient support and will be able to perform its job effectively. If there are any noticeable malfunctions, take note so it can be resolved.
7. Check for Corrosion:
After examining the pipes, double check that there isn’t any corrosion on the sprinkler heads themselves. If there appear to be any sprinkler heads with discoloration, peeling exterior, or rust, replace those heads promptly.
8. Perform Functional Testing:
At least annually, conduct functional tests on all fire sprinkler systems to ensure proper operation. To do this, activate the trigger system to confirm that the water flows as intended. However, be cautious before performing this step. It may be necessary to communicate with other personnel and inform them of the pending test before activating the system.
9. Inspect Water Supply:
Additionally, check the water supply to the sprinkler system. After all, without a sufficient supply of water, the system is unable to fulfill its duty during a fire emergency. To check the water supply, open the control valves and examine supply lines for visible damage or leakage. Also test the main drain, review the integrity of the riser, and look over the water pressure gauge. These instruments will provide valuable information about the overall state of the fire sprinkler system.
10. Review Alarm Systems:
Another key action item while inspecting a fire sprinkler system is to verify the proper functioning of alarm systems. This includes audible alarms and communication systems alerting occupants or emergency services. Test to make sure that they go off as needed, have working batteries, and could be used in an emergency.
11. Documentation and Reporting:
While often downplayed as a “boring” part of the job, documentation and reporting are actually crucial to the upkeep of fire sprinkler systems. During an inspection, it is important to take notes on the inspection results, any issues discovered, and actions taken. Upon completion of the inspection, it is imperative that this rich information be added to company reports. Why? Maintaining detailed records will be helpful for demonstrating compliance and for future reference regarding system well being.
12. Schedule Regular Inspections:
Finally, establish a routine inspection schedule. Regular inspections contribute to ongoing system reliability. Having a schedule will ensure that inspections are conducted in a timely fashion and also promote compliance by routinely checking that everything is in order.
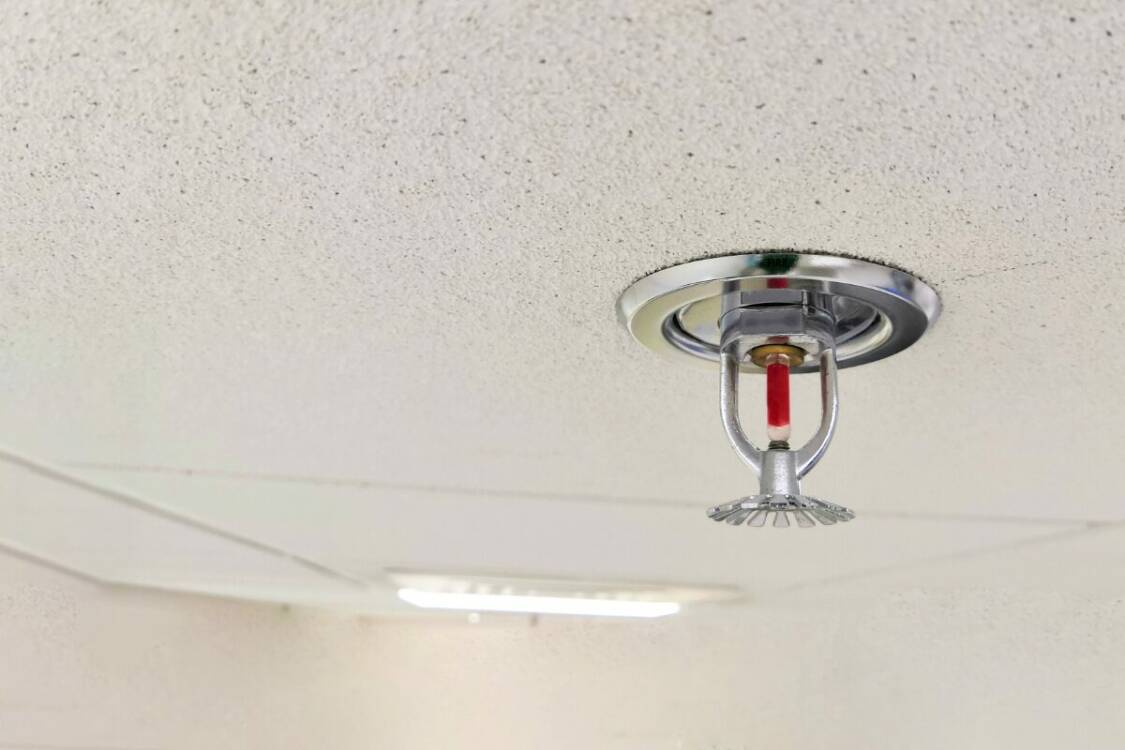
How Often Should Fire Sprinkler Systems Be Inspected?
There are different levels of inspection that are needed for fire sprinkler systems. Here is what you need to know to stay on top of the inspection requirements.
- Monthly Inspections:
- Check control valves to ensure they are in the fully open position.
- Inspect gauges for normal pressure readings.
- Verify that there are no visible signs of physical damage or leaks.
- Quarterly Inspections:
- Conduct a more detailed inspection of gauges and control valves.
- Inspect alarm devices to ensure they are free from physical damage.
- Verify that all gauges, valves, and alarm devices are labeled correctly.
- Annual Inspections:
- Perform a complete inspection of the entire sprinkler system.
- Check all components, including pipes, fittings, hangers, and sprinkler heads.
- Conduct a flow test to ensure water flows as expected.
- Verify the hydraulic nameplate information.
Additional Inspections
There are cases in which the traditional schedule of fire sprinkler inspections is not sufficient. Here are some scenarios when additional inspections might be needed.
- Internal Inspections:
- Conduct internal inspections of sprinklers in certain environments as specified by NFPA 25.
- Replace sprinklers that show signs of corrosion, damage, or aging.
- Antifreeze Solutions Inspection:
- If antifreeze solutions are used, inspect them annually.
- Verify the concentration levels and replace or add antifreeze as needed.
- Control Valve Inspections:
- Inspect control valves for proper operation and condition.
- Verify that valve supervisory devices are functioning correctly.
- Post-Fire Inspection:
- After a fire event, inspect the entire sprinkler system to identify any components that may need replacement or repair.
- Document any damage caused by the fire and take corrective actions
Building Manager’s Role in Fire Sprinkler System Inspections
Building managers are an essential part of maintaining fire sprinkler systems. In order to best do their job, managers should make sure to stay informed on the most recent regulatory requirements, industry best practices, and more. Additionally, they should understand what kind of fire sprinkler system(s) they have in the building, the inspection requirements for that system, and what servicing that system has received. This kind of information will allow them to best set an inspection schedule, perform adequate maintenance, and ensure that the fire sprinkler system(s) is up to code. By taking these steps, building managers are able to proactively participate in creating a safe environment and minimizing the likelihood of a fire emergency occurring.
While building managers can and should conduct weekly/monthly visual inspections, it is recommended that a licensed and trained fire sprinkler professional be hired and brought in to conduct the actual fire sprinkler system inspections (quarterly, annually, 5 year, etc.) and testing. A professional brings with them expertise and knowledge that will aid in identifying potential problems, conducting inspections efficiently, and correctly handling equipment. When choosing an inspector to work with for this, look for a reputable and experienced fire inspection company. This will help ensure that the inspections are done right, equipment is well taken care of, and NFPA 25 standards are followed.
How to Utilize Fire Sprinkler Software in Inspections
InspectNTrack software simplifies fire sprinkler inspections by offering timelines that show when the last inspection was performed and when the next one is needed. In this way, the software removes the challenge of keeping up with various timelines and manually updating a schedule. The system does it all for you! That way, there’s no stress about managing dates or tracking time.
Additionally, our inspection software offers the ability to use pre-made NFPA inspection questions or create custom question sets that best fit your organization’s needs. These allow the inspectors to check for compliance and perform thorough inspections, making the most of safety efforts.
While performing inspections, the software user has options such as adding an image or taking notes. These features are useful for documenting any areas that need further attention, while also demonstrating regulatory compliance. With features like this, it is easy to keep track of necessary maintenance as well as what equipment is functioning properly.
As the inspection is performed, all new data is immediately updated to the cloud system. This means that on-the-go reporting is possible with or without wifi. Not only that, but the inspection data becomes readily available, meaning that any company management or team members can easily access needed information. This enables teams to effectively communicate and collaborate.
All of these features make it simple to show compliance in the case of an audit. The paper-free centralized data platform gives you one place to go to to find all program information. Since InspectNTrack’s software includes a detailed audit history, the program manager can see all inspection efforts that have been made, who performed the inspections/maintenance/testing, and when they were completed. By using software for data collection and storage, the entire process of managing a fire and life safety program is made a lot more achievable.
For more information about how InspectNTrack software can help run a fire safety program or perform fire sprinkler system inspections, talk to one of our specialists! They are happy to answer all questions about the product, its usage and implementation, pricing, and more. Click here to request a demo.
Conclusion
Fire sprinkler systems are powerful tools for fighting fires and promoting building safety. In order to keep these systems functioning properly, regular inspections need to be performed. Before performing an inspection, individuals should become educated on current regulations, inspection frequency, and other relevant topics. Trained professionals can follow along with the steps outlined in this article as they inspect and test fire suppression systems. For a proper inspection, inspectors need to do some initial prep work, perform thorough inspections of all parts of the fire sprinkler system, and then adequately report and document their findings. InspectNTrack offers software to simplify the process of performing fire sprinkler system inspections. For more information on InspectNTrack software, request a demo!