In this article we’ll examine the complexities associated with managing fire extinguisher inspections and maintenance, common methods used, and ways that moveable equipment technology helps to overcome challenges.
Fire Extinguisher Maintenance and Inspection Requirements
Fire extinguishers are one of the trickiest types of fire safety equipment to maintain because they require managing multiple different task types and because they can move around a facility. According to NFPA 10, all fire extinguishers require a monthly inspection and an annual maintenance. Beyond that, there are additional fire extinguisher maintenance tasks required that vary based upon agent type. These tasks can include hydrostatic testing at 5 year or 12 year intervals, 6 year maintenance tasks, cartridge changes, hose conductivity tests, and more. The specific timing for when the fire extinguisher maintenance tasks should be performed is determined based upon the manufacture date of the fire extinguisher and/or the last time the task was performed.
Why Fire Extinguisher Maintenance is Hard to Track
Typically, a company buys and replaces fire extinguishers systematically over the course of years or even decades. As a result, the fire extinguishers located throughout a facility have all different manufacture dates. This means that they also have all different maintenance schedule requirements. Unlike a monthly inspection or annual maintenance that can be conveniently scheduled for all fire extinguishers at the same time, fire extinguisher maintenance is customized to the age of the unit and is an ongoing process to manage.
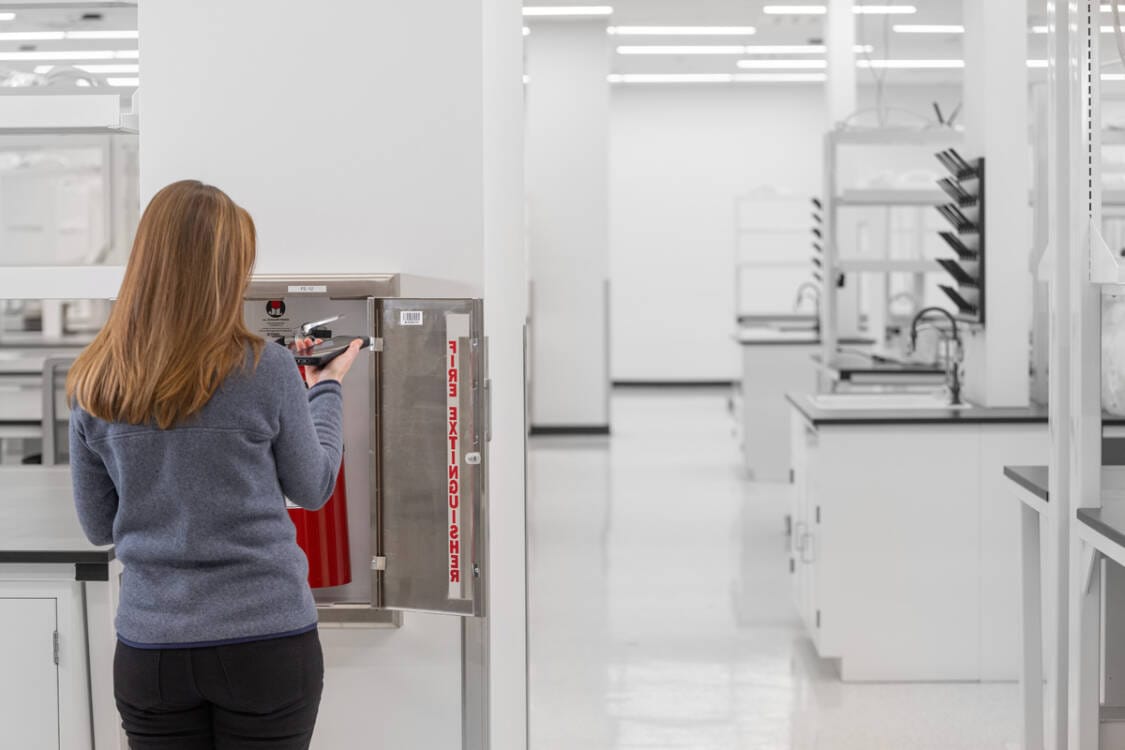
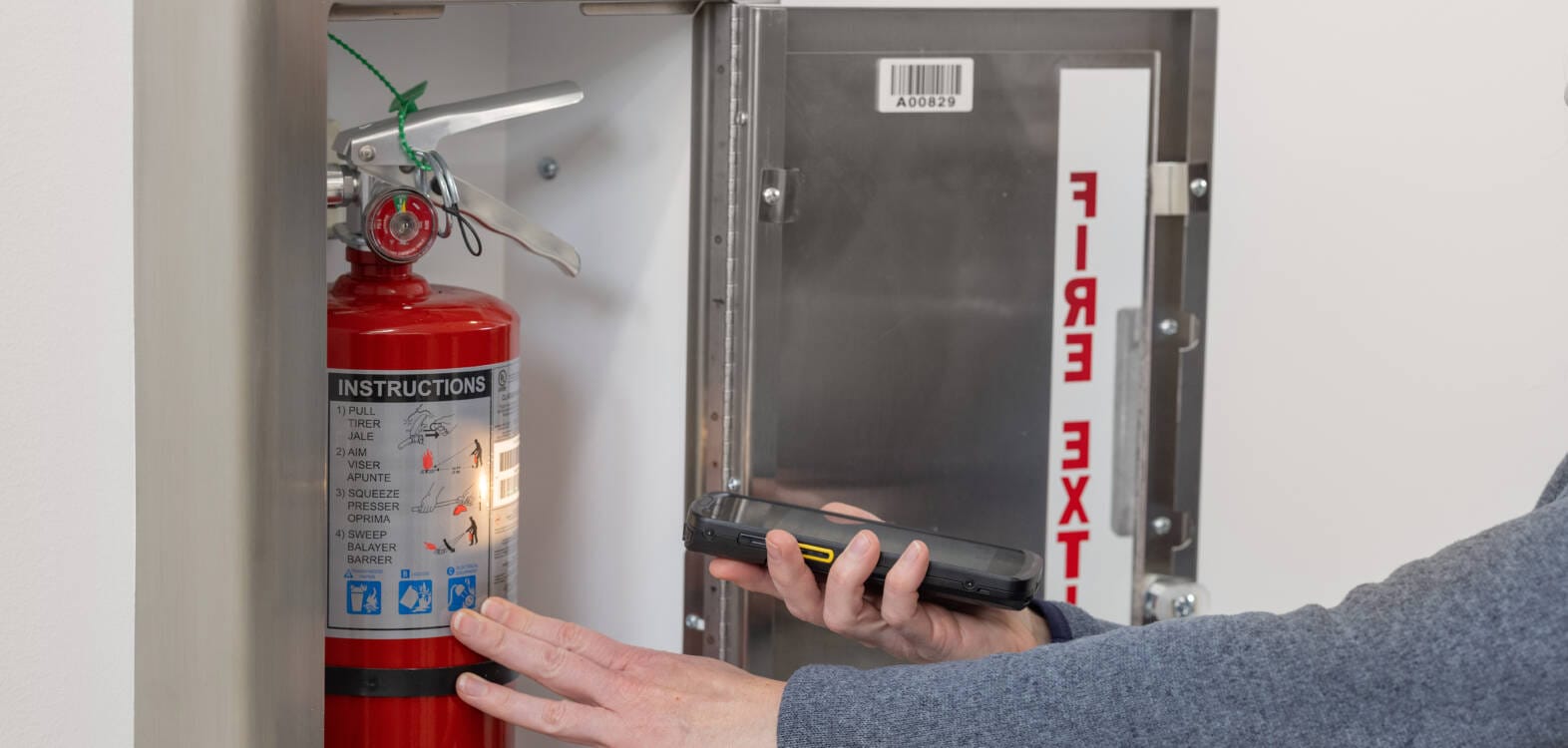
Ways to Manage Fire Extinguisher Maintenance
There are a few common ways that companies manage fire extinguisher maintenance schedules.
Rely on a Contractor or Service Company
Some companies take the stance that they will trust a contractor to manage fire extinguisher maintenance for them. The contractor visits the facility at agreed upon intervals. During this time, the contractor walks around and looks for fire extinguishers needing maintenance. Identified extinguishers are removed from service and taken back to the contractor’s shop for maintenance, then returned back to the facility when complete.
Pros: This requires little to no work from the company.
Cons: This is rarely an accurate method for maintaining compliance. Contractors do the best they can to find the fire extinguishers which need maintenance, but frequently miss some of the equipment. When an AHJ audit reveals non-compliant fire extinguishers, blaming it on a contractor is not an acceptable excuse and does not prevent fines or accreditation complications.
Keep Track of Dates Manually
Many companies work to augment the services provided by a contractor with proactive management of fire extinguisher maintenance dates. This generally includes recording the maintenance last done dates in a spreadsheet. Since spreadsheets can be hard to manage, companies who use this process also add an extra step to the monthly fire extinguisher inspection which includes checking the verification of service sticker on each extinguisher to determine if maintenance is required. This greatly increases compliance but adds a ton of extra manual time and effort to the monthly inspection.
Pros: Companies who actively track their fire extinguisher maintenance dates can budget for upcoming fire extinguisher maintenance because they know which services are due and for how many fire extinguishers. They can also ensure that the contractor is getting everything done. They can more readily provide proof of compliance when audited.
Cons: The fire extinguisher maintenance records are kept manually and prone to human error. If a fire extinguisher is moved from one location to another, the records must be manually updated or they become inaccurate. For example, imagine a dry chemical fire extinguisher manufactured in 2020 is in service. It’s first maintenance task is due in 2026. Now imagine that the extinguisher is discharged and subsequently replaced by a spare which was manufactured in 1996 and is due for maintenance this year. Unless someone manually updates the records to account for the new extinguisher being removed and the spare being moved into service, the records are instantly inaccurate. The contractor might arrive and look for the fire extinguisher that needs service in the spares stock, but give up when it is not found. Now we have a fire extinguisher that is past-due for maintenance located in an in-service location and nobody knows it. This presents numerous safety and compliance concerns.
Use Standard Fire Inspection Software
Barcode driven fire inspection software offers a huge step up from spreadsheet tracking. A barcode can be applied to each location that holds a fire extinguisher, and details about the fire extinguisher including maintenance and inspection dates are added to the software. Inspection and maintenance dates are updated digitally after scanning the location barcode.
Pros: Digital records offer much greater accuracy and reduce human error. The software is able to provide reports showing when inspections and maintenance tasks are due, and can report on tasks that are past-due or missed. Compliance is quicker and easier to report on.
Cons: When a fire extinguisher is moved, as in the example above of the discharged dry chem, standard fire inspection software still requires manual intervention to update records. Depending upon the software program, this can range from pressing buttons in an app to manually move the fire extinguisher, or editing the location to delete the discharged fire extinguisher and setup the spare in its place. This often causes companies to go to great lengths to label fire extinguishers and locations with matching numbers so that when maintenance is performed the fire extinguishers can be returned to the same exact location to avoid editing. This is a lot of extra physical effort to avoid having to make edits to the software records.
Use InspectNTrack Fire Inspection Software with Moveable Equipment Technology
InspectNTrack’s patented moveable equipment technology takes a totally different approach to fire extinguisher management. Within InspectNTrack, every fixed location that holds a fire extinguisher (bracket, cabinet, etc.) is barcoded and added to the software. Fire extinguishers each get their own different barcode. Then, fire extinguishers are associated to locations. Each time an inspection is performed, both the location and the extinguisher barcodes are scanned. If the combo matches the system records the location is verified and the inspection can be performed. If the extinguisher has moved the software will automatically relocate the fire extinguisher and add the location change to the inspection report.
Pros: Full automation! With this setup a company will never have to edit or manually relocate an extinguisher again. Full inspection and maintenance records are associated to the fire extinguisher, not the location. When a fire extinguisher is moved, InspectNTrack recognizes the move after the barcodes are scanned and updates the location automatically without manual intervention.
Cons: It can be extra effort to set the system up initially, but a return on time investment is quickly achieved once the inspection and maintenance program begins.
How to Update Records After a Contractor Performs Fire Extinguisher Maintenance
When contractors take fire extinguishers offsite for maintenance and subsequently return them, this creates additional workload to manage. Let’s look at the different requirements with each program option.
Rely on a Contractor or Service Company
There are no additional data entry requirements since internal records are not kept. The company must simply pay the contractor’s bill and hope that it was accurate.
Keep Track of Dates Manually
When records are maintained in Excel, the contractor’s service report must be matched up against the Excel spreadsheet. The maintenance dates must be manually updated for each individual fire extinguisher. This can be a tedious and time-consuming task.
Use Standard Fire Inspection Software
Methods for updating fire extinguisher maintenance dates can vary from system to system, but often include a manual workflow that must be followed.
Use InspectNTrack Fire Inspection Software With Moveable Equipment Technology
InspectNTrack’s Quick Inspect workflow allows the user to setup the parameters of the type of maintenance work that was done (hydrostatic test, 6 year maintenance, etc.). Once fire extinguishers are returned, simply turn on Quick Inspect and start scanning the fire extinguisher barcodes in combination with a location barcode. The scans will simultaneously move the fire extinguisher from the contractor’s location to the new location (in-service or spares) and update the maintenance date for the selected task. There is absolutely no editing or manual work required. Fire extinguishers can be placed in ANY location and do not need to be returned to the original location.
But what if the contractor puts the extinguishers back and you don’t get the opportunity to scan? No worries, InspectNTrack’s Bulk Update feature offers a shortcut to apply the maintenance task and date to all the fire extinguishers at once within the web portal.
InspectNTrack Software
Want to learn more about what InspectNTrack is and how it can help optimize your fire extinguisher maintenance and inspection tracking? If so, connect with our team by requesting a demo! Our team of specialists are happy to set up a meeting to help you determine if InspectNTrack software is right for your company’s needs. We believe in the power of our product to change the way safety is approached in the workplace and want to answer any questions you have. You may have come looking for fire extinguisher maintenance software, but InspectNTrack can do a whole lot more than that. We have a multitude of solution offerings, and hope that you will give us the chance to show just what InspectNTrack can do!
Conclusion
For companies that manage fire extinguisher inventory, InspectNTrack’s moveable equipment technology remains the superior choice for automating the previously manual aspects of inspection and maintenance tracking. Inspection and maintenance dates are tied to the fire extinguisher, not the location, to ensure consistent accuracy in records.