Performing Eyewash Inspections
Eyewash stations are an essential piece of equipment for workplace safety. They are key in providing immediate relief to employees exposed to harmful chemicals or substances.
Regular inspections ensure that these stations are always ready in an emergency and compliant with safety standards. This can be especially important for workplaces with higher exposure risks, such as laboratories, chemical processing plants, and manufacturing facilities.
In this article, we will dive into eyewash station inspections and provide a step-by-step guide for completing them. The steps will cover everything from initial preparation to documentation and maintenance, making it that much easier to inspect and maintain eyewash stations.
Eyewash Stations: The Basics
Before diving into the details of inspections, it’s important to understand what an eyewash station looks like and how it is used.
Purpose of eyewash stations:
Eyewash stations are a form of fire safety equipment used to provide relief in the event of an accident or injury to a person’s eye(s) or face. They are a means of reducing damage until a medical team can come and inspect the injured person. As such, they are a common piece of equipment in many areas involving construction, chemicals, or general building safety.
Identifying eyewash stations:
In order to identify an eyewash station, it is key to understand what it looks like. There are 2 main types of eyewash stations: portable and plumbed. Portable eyewash stations generally look like a plastic cube or box with a handle. As for plumbed eyewash stations, there are a few different kinds. Plumbed ones can have a pedestal, be wall-mounted, be sink-mounted, and even come as a combo unit with safety showers. Regardless, eyewash stations usually resemble a water fountain in that there is a bowl area for excess water along with spout(s) that water flows from.
Though there are a variety of eyewash station types, this article will give detailed but also generalizable steps that can be followed when completing inspections.
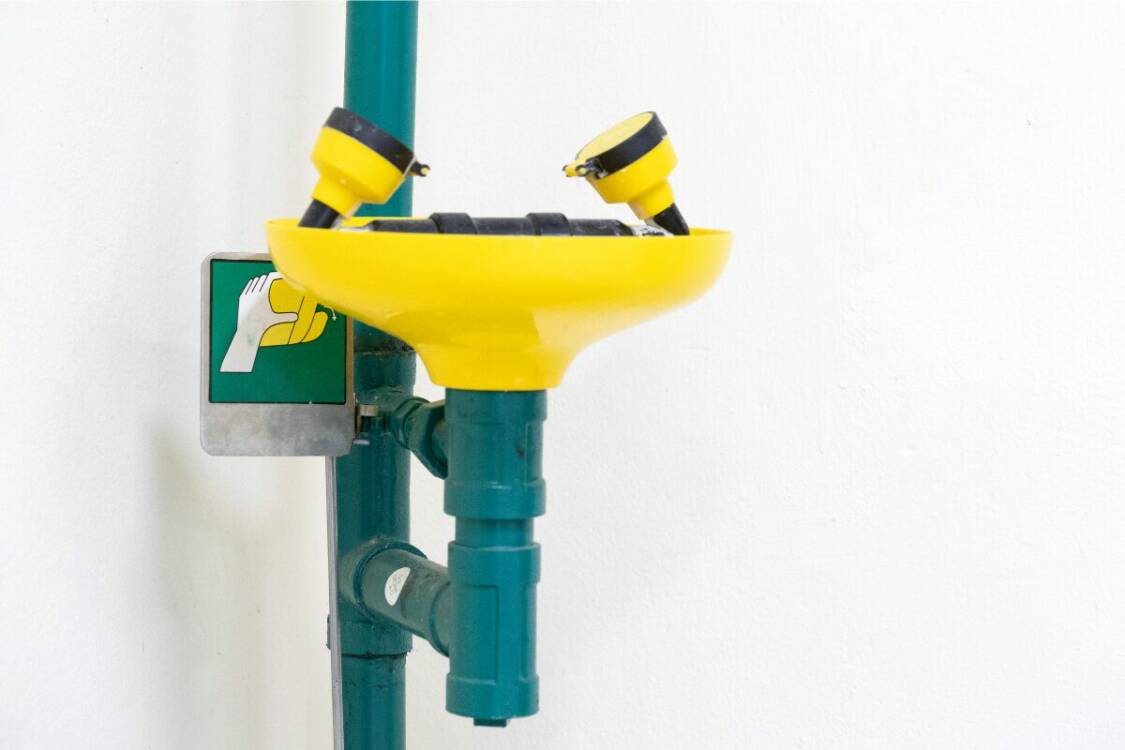
Inspection App Solutions
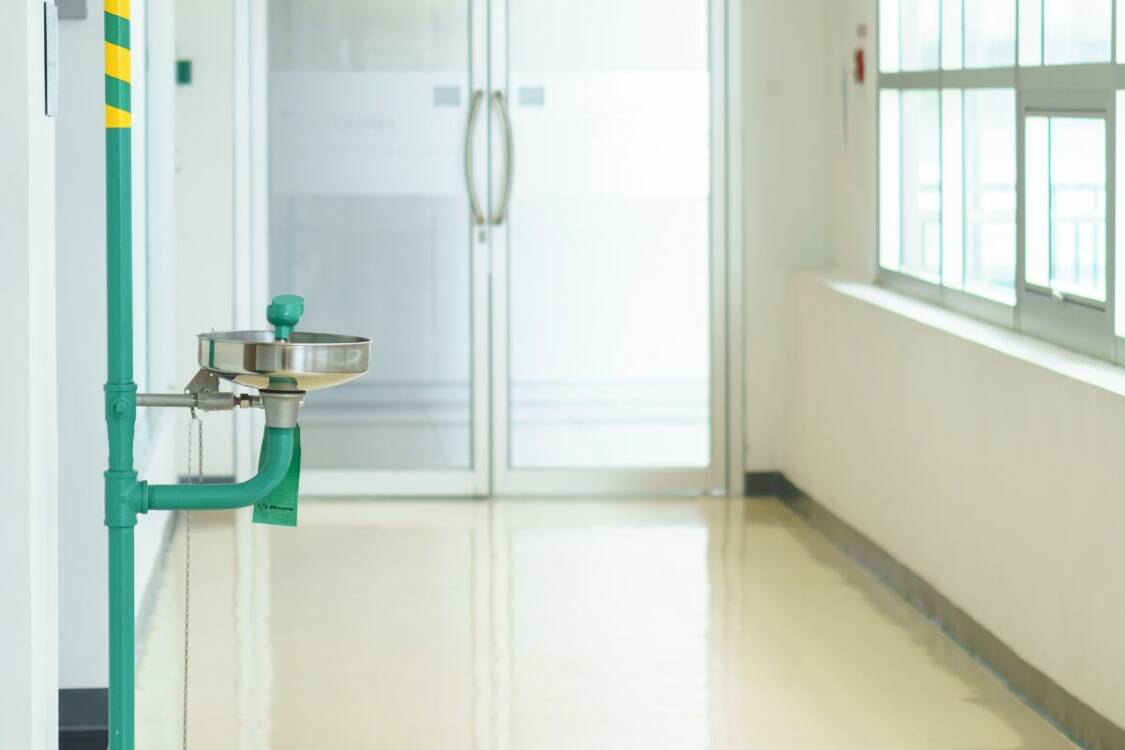
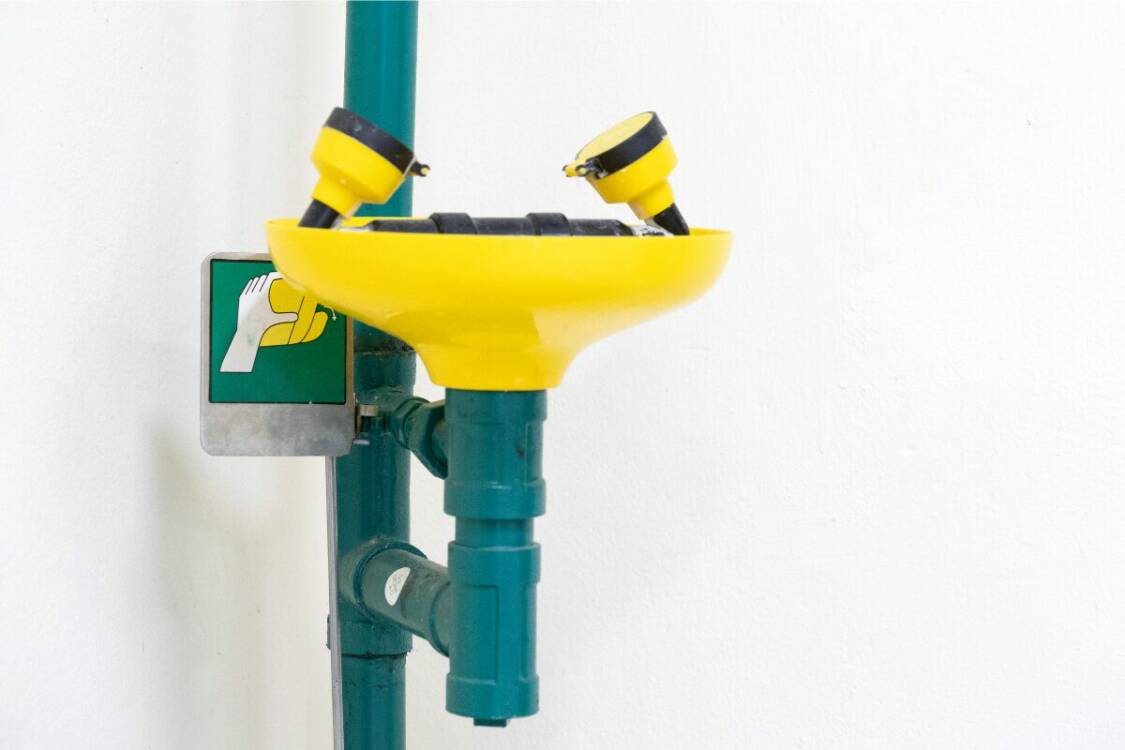
The Importance of Eyewash Station Inspections
Regular eyewash station inspections offer a range of benefits to both users and building owners. Here are some of the primary reasons that inspections should be a focus:
- Relief during emergencies: Eyewash stations are critical in helping prevent long-term eye or face injuries after exposure to chemicals or other irritants. A properly functioning station can reduce the severity of injuries and ensure workers have immediate access to clean, uncontaminated water in emergencies.
- Equipment Upkeep: If stations aren’t properly maintained, employees may face risks such as exposure to harmful bacteria or mineral buildup in stagnant water, inadequate flow, or incorrect water pressure. Negligence can lead to a shorter lifespan of equipment and the need for more frequent, costly replacements.
- Regulatory Compliance: Inspections are a requirement for compliance with the established standards set by OSHA and ANSI. Those who do not meet the regulatory requirements may be subject to fines, citations, and other penalties.
As these bullet points suggest, eyewash stations inspections play a key role in emergency preparedness. Often, these inspections fit into a broader safety and emergency response plan meant to promote readiness and minimize risk. By proactively participating in their upkeep, inspectors help to ensure that eyewash stations can perform at their highest level and offer the safety insurance they are supposed to.
Compliance Standards to Know About
One of the fundamental reasons for performing eyewash station inspections is to ensure their compliance with the established regulations and safety standards.
Within the United States, both OSHA and ANSI are governing bodies for workplace safety. Both of these organizations have established guidelines for the care and inspecting of eyewash stations. This section provides an overview of the 2 main standards that apply to eyewash stations, OSHA 1910.151(c) and ANSI/ISEA Z358.1.
OSHA mandates that eyewash stations be readily available and operational in any workplace where workers could be exposed to harmful chemicals, corrosive materials, or other eye hazards.
OSHA’s regulations, specified in 29 CFR 1910.151(c), require employers to ensure that eyewash facilities are within immediate reach—typically within a 10-second walk—for employees exposed to hazardous substances.
While OSHA does not provide specific inspection details, it references ANSI/ISEA Z358.1 as the accepted industry standard for equipment requirements. This includes ensuring that eyewash stations are inspected and tested weekly to confirm consistent water flow, functionality, and easy access. Additionally, OSHA emphasizes that stations must be maintained to deliver tepid water (60°F to 100°F) to avoid further injury and meet the critical flow rate requirements to fully flush the eyes in an emergency. Employers are also required to train workers on the location and use of eyewash stations as part of their safety protocol.
ANSI/ISEA Z358.1 outlines essential requirements for eyewash station inspections, designed to ensure that emergency equipment is functional, accessible, and ready to use at all times.
According to the standard:
- Eyewash stations must be inspected and activated weekly to verify proper operation, including flow rate, water temperature, and accessibility.
- The flow rate should meet a minimum of 0.4 gallons per minute (GPM) and be hands-free, allowing continuous operation for at least 15 minutes.
- Water temperature must fall within a safe range of 60°F to 100°F to avoid further injury to the user’s eyes.
- The eyewash station must also be located within a 10-second reach from potential exposure hazards, marked with clear, visible signage, and easily accessible with an unobstructed path.
Comprehensive annual inspections are required to confirm ongoing compliance with ANSI/ISEA standards and ensure that nozzles, covers, and other components are free from obstructions, mineral deposits, or other issues that could inhibit proper function.
Who Should Perform Eyewash Station Inspections?
Weekly flow testing can be performed by managers or other employees.
As was just mentioned, eyewash stations should be tested weekly to verify the flow and keep the water from becoming too stagnant. This is a job that can be performed by a building manager or other worker. It requires little skill or knowledge, making it a task that can generally be performed by anyone on the job.
Annual inspections should be performed by a hired inspector or individual who is well informed and familiar with the inspection requirements and process.
Safety standards require eyewash stations to be given an in-depth review at least annually. These inspections are much more thorough than the weekly flow tests, and therefore require a higher level of expertise. Because these are performed to meet the regulation requirements, they also must be documented carefully in order to prove compliance during an audit.
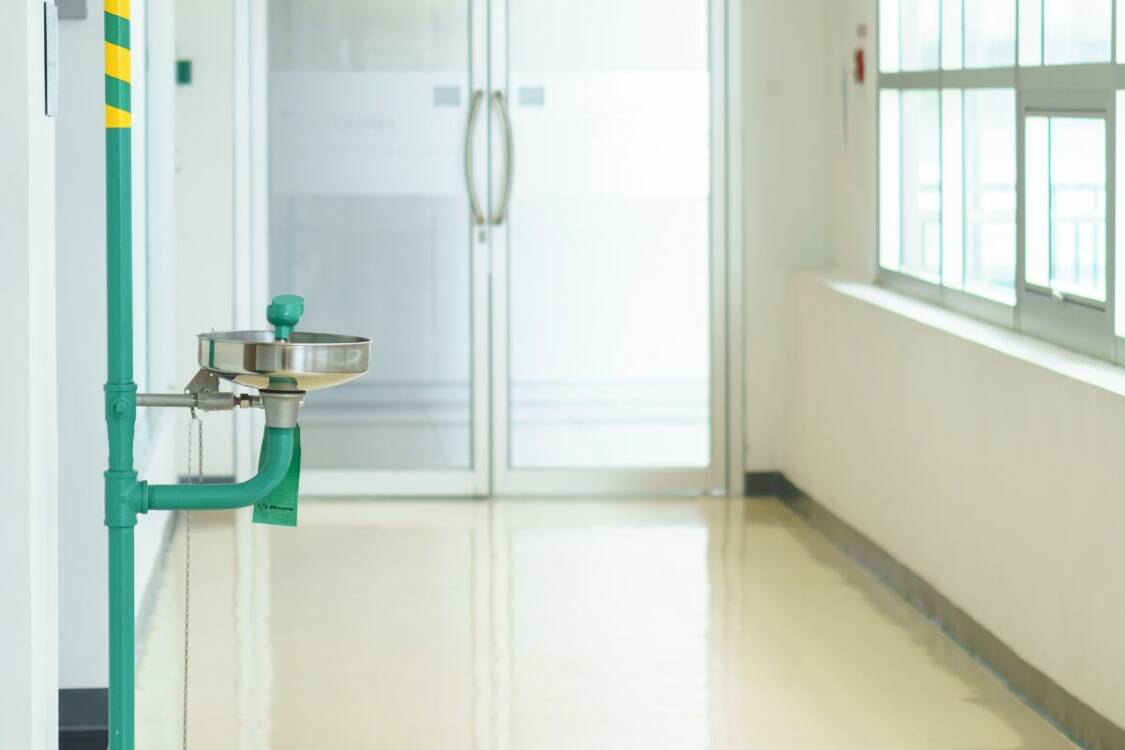
10 Steps for Eyewash Station Inspections
Performing an eyewash station inspection, especially the first few times, can feel intimidating. Thankfully, the process can be broken down into 10 simple steps. Follow these steps to complete a thorough eyewash station inspection and ensure it’s always ready for use.
1. Understand Inspection Requirements
It is vital that anyone who is performing an eyewash station inspection be well versed in the industry standards and updated on the most recent regulation guidance. Inspectors should familiarize themselves with ANSI/ISEA Z358.1 and OSHA 1910.151(c), along with any other applicable information.
Even inspectors who regularly perform eyewash station inspections should be mindful to regularly check safety standards. Doing so can freshen their memory on the specifics of requirements related to the water flow, temperature, spray pattern, installation height, etc.
2. Gather Essential Tools and PPE
Next, gather the necessary materials for completing the inspection.
- Tools: Thermometer, stopwatch, flow test gauge, cleaning supplies, and possibly a flashlight to check interior parts.
- PPE: Gloves, goggles, and any other necessary protective gear, especially in areas with hazardous materials.
These elements will help to protect the personnel performing the inspection while also measuring key information such as the water temperature, rate of flow, and ability to continuously flow for at least 15 minutes.
3. Check Station Accessibility and Visibility
As stated in the ANSI standard, eyewash stations should be accessible within 10 seconds for an injured person. Here are some things to look for to check off that requirement.
- Pathway: Ensure the path to the eyewash station is clear and unobstructed. There should be no barriers, and the station should be accessible within a 10-second reach of any potential exposure area.
- Signage and Lighting: Verify that the station is marked with clear, visible signage, according to ANSI standards, and that it’s well-lit. This will help anyone to recognize its location and find it in an emergency.
Having an eyewash station is no good if it can’t be reached or found in a time of need. This inspection step certifies that the equipment can be of use, should that be necessary.
4. Activate the Eyewash Station
Now, you can begin the operational testing of the eyewash station.
Start by turning on the eyewash station to verify that it operates smoothly and promptly upon activation. Eyewash stations generally have two water nozzles, one on each side of the bowl, that should produce water that flows in opposite directions towards each other, creating a stream that meets in the middle.
Check that the water is flowing continuously, overlapping in the middle, and that it operates without users having to hold down the lever. This way, the equipment can be used with hands-free operation, which is crucial since users generally need their hands for holding their eyes open during rinsing.
5. Test the Water Flow and Spray Pattern
Next, you can get into the specifics of the water flow. The goal of this step is to validate that the water meets the standards for effectiveness in removing chemicals or other harmful substances from the eye or skin.
- Flow Rate: Use a flow test gauge to check that the station provides a minimum flow rate of 0.4 gallons per minute, as required by ANSI standards.
- Spray Pattern: Observe the water flow to confirm it delivers an even, consistent stream that covers both eyes simultaneously. Adjust if necessary to ensure optimal coverage.
- Pressure: Confirm that water pressure is adequate but not too forceful, as excessive pressure could harm the user’s eyes.
6. Check Water Temperature
Water that’s too hot or cold may discourage station use or even exacerbate injuries. Because of this, it is essential that the water temperature fall between a temperate range. Test to be sure that the water is a comfortable temperature for use.
Using a thermometer, measure the water temperature to ensure it falls between 60°F and 100°F. This is the recommended range provided by ANSI.
7. Flush the System to Remove Stagnant Water
If the eyewash station isn’t regularly tested (weekly), this can leave the system vulnerable to stagnant water which can develop bateria and become unusable in an emergency event. This step ensures the sanitation quality of the water, so that it is a helpful agent rather than a hindrance to someone needing help removing chemicals from their face.
To complete this step, allow the station to run for at least one minute to flush any stagnant water. This helps remove any bacteria or buildup that could accumulate, especially in infrequently used stations.
Inspect the water quality to ensure it’s clear and free from contaminants. Cloudy or discolored water can signal a need for pipe flushing or filter replacement.
As the water flows, observe the drainage system to ensure that water flows away correctly, without pooling or spilling onto the floor.
8. Inspect the Nozzles for Cleanliness and Functionality
Next, take a minute to check the nozzles for any signs of clogging, mineral deposits, or other blockages. Mineral buildup can obstruct water flow, and debris in nozzles may reduce the effectiveness of the eyewash.
Clean the nozzles and any covers as necessary to ensure a clear flow of water. Additionally, make a note if there are any issues or parts of the eyewash station that need to be replaced.
9. Document Inspection Findings
Throughout the inspection, be taking notes on the functionality of the system. Record key details of the inspection, including the inspector name, date, time, water temperature, flow rate, and any observed issues or repairs. Note any parts that may require replacement, such as valves, nozzles, or drainage components, and arrange for necessary repairs promptly.
This step, while it may seem tedious, is IMPERATIVE. Documentation helps maintain a historical record of maintenance and ensures compliance with regulatory bodies and can be used during audits.
Often the reporting isn’t complete when the inspection is done, so it is extremely important to finish the report and file it somewhere where it can be retrieved later for audits.
10. Report and Address Any Issues
Finally, if you identify any issues, such as inconsistent water flow, unclear water, or malfunctioning parts, report them immediately for corrective action. These items should be included in the documentation of the inspection, but they will require steps to remedy them. Make sure that plans are in place to address any issues found and that repairs are completed quickly. Re-inspect the eyewash station after a repair to verify that it meets safety standards.
Common Inspection Issues and How to Address Them With Software
Here are some common issues related to eyewash station inspections to be aware of:
Insufficient Training
Problem: A lack of knowledge about eyewash stations or the inspection process leads to incomplete or improper testing and review.
Solution: To avoid this issue, companies should provide initial training to employees during the onboarding process as well as an annual refresh. Software can be especially helpful for training, as there are a variety of online tools such as videos and images that can enhance the training process. Our software comes equipped with a knowledge base within the platform that provides users with access to a variety of materials that can be useful in training.
Incomplete Documentation/Records
Problem: Documentation is needed to prove compliance during audits. When reports are missing or unfinished, this can be problematic for avoiding OSHA fines.
Solution: In order to avoid incomplete records, encourage workers to set aside a few minutes after each inspection to finish their report(s). Software can assist in this process by providing a step by step walkthrough of inspection procedures and sending completion reminders.
Unaddressed Issues/Repairs
Problem: Repairs and part replacements are inconvenient and therefore often get put on the backburner. However, procrastination in fixing safety equipment can lead to severe consequences during emergencies.
Solution: Software can help reduce the delays for repairs on equipment by sending action triggers that remind users of the necessary action that is yet to be taken.
Utilizing Software for Inspections
Though investing in software does come with some costs, the benefits that it offers far outweigh the costs in terms of improved efficiency, compliance, and saved resources. Not only does software simplify record-keeping and scheduling inspections, but it also can streamline the entire inspection process.
Here are some of the top features that make InspectNTrack the go-to software for eyewash station inspections:
- Mobile App – Our software is usable on virtually any device! Anything with iOS, Windows, or Android should work.
- On-the-go Reporting – No wifi? No problem. All data is uploaded and saved to the cloud.
- Organized Documentation – All your data is stored in one place, making it easier to manage.
- User Friendly Interface – Even new users can quickly learn the software and implement it effectively into their work.
- Dynamic Scheduling – The system can be used to schedule upcoming inspections and maintenance, making it that much easier to stay on top of compliance requirements.
- Action Triggers – Our system offers alerts to help notify users of needed action. This way, nothing gets overlooked.
These features function to make the inspection process smoother for the inspector as well as more efficient for the company. Some additional benefits of using software for inspection include improved transparency, increased accuracy, and overall improved workplace safety.
For more information about our software solution, schedule a demo with one of our specialists! They are happy to answer questions and provide information so you can determine whether or not our software is the right fit for your company’s needs. We are confident in the power of our product to change the way safety is approached in the workplace and want to answer any questions you have. You may have come looking for eyewash station inspection software, but InspectNTrack can do a whole lot more than that. We have a multitude of solution offerings, and hope that you will give us the chance to show just what InspectNTrack can do!
Conclusion
Conducting eyewash station inspections is a critical component of any workplace safety program, especially in environments where exposure to hazardous materials is possible. By following the steps above and adhering to OSHA and ANSI/ISEA Z358.1 standards, companies can ensure their eyewash stations are functional, accessible, and ready for immediate use. Regular inspections protect workers, improve compliance, and contribute to a proactive approach to safety management. For organizations that want to further improve their safety inspections, software is a valuable tool to consider. By making intentional efforts to maintain eyewash stations, companies engage in cultivating a safer future.