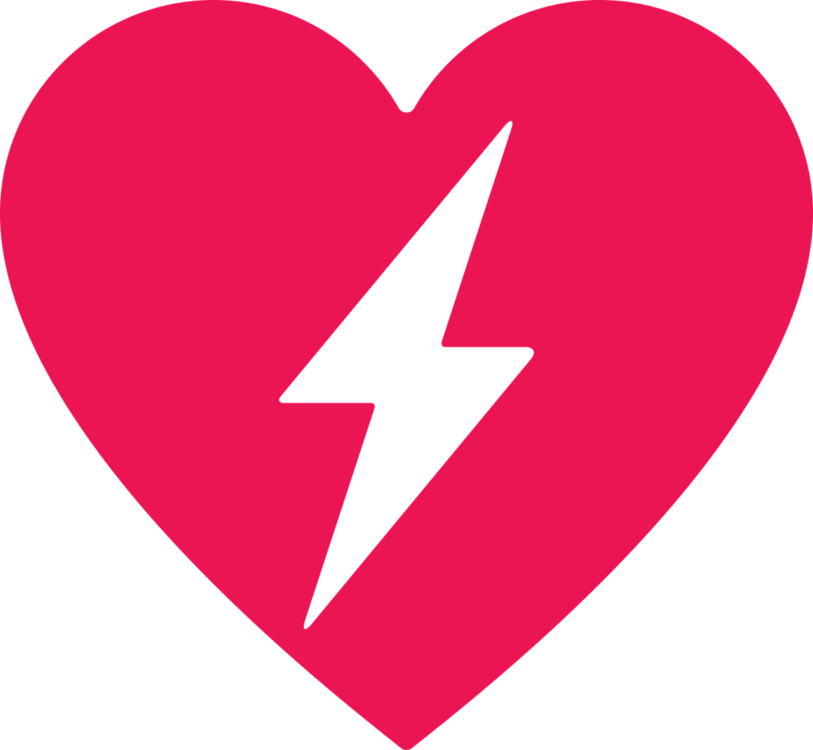
An AED is an invaluable tool for saving lives IF it works properly in an emergency. This article explores what AEDs are, how they should be maintained, and how InspectNTrack software can help efficiently manage AED inspection programs.
Are Your AEDs Tested, Maintained, and Ready to Save Lives?
On January 2, 2023, NFL safety Damar Hamlin went into sudden cardiac arrest on the field during a Monday night football game. Millions of people watched in horror as first responders tried to revive him. CPR was performed, but ultimately it was the use of an AED (Automated External Defibrillator) that reset his heart rhythm and stabilized him until he could be transported to the hospital.
AEDs are things that people might have previously casually recognized hanging on the wall in public places or might have looked past altogether. Damar Hamlin’s tragic event had one positive outcome: over 23 million viewers witnessed his injury and then subsequently witnessed his miraculous lifesaving effort which included the use of an AED. This had the effect of bringing AEDs into the spotlight as an invaluable lifesaving tool.
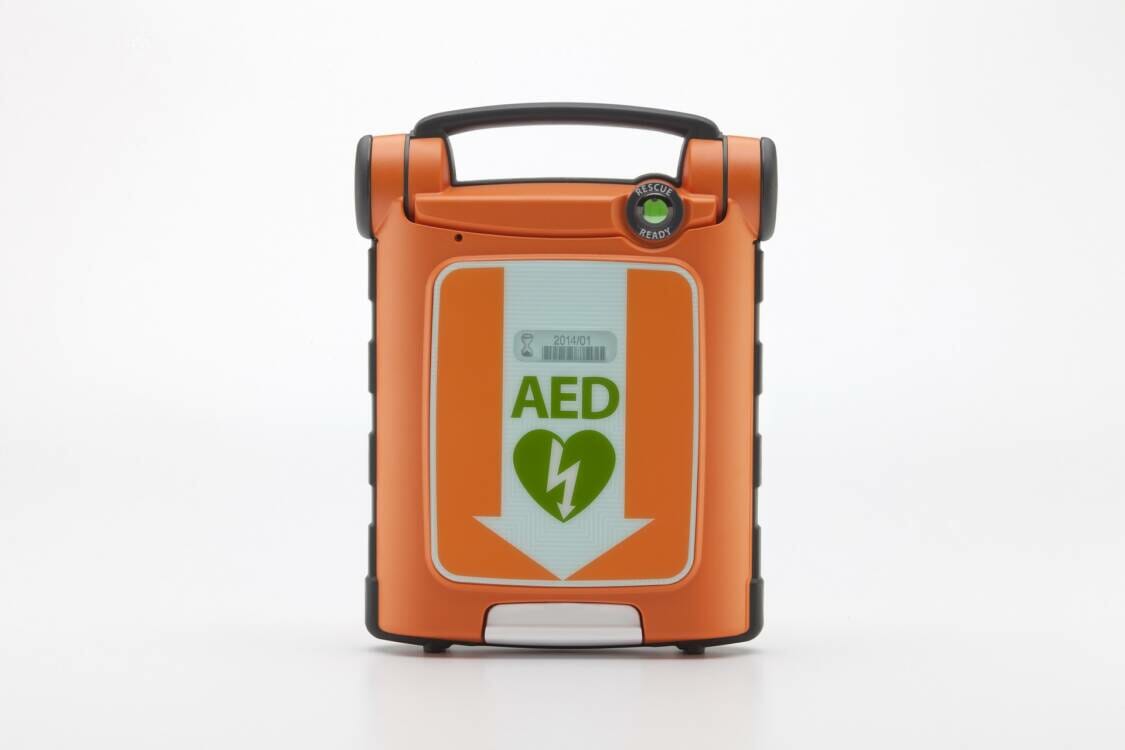
Why Are AEDs Important?
The use of an automated external defibrillator (AED) in the event of sudden cardiac arrest can significantly increase the chances of survival. According to studies, the survival rate for people who receive defibrillation within the first few minutes of cardiac arrest can be as high as 74%. The survival rate decreases by 7-10% for every minute that defibrillation is delayed. Survival rates are also influenced by the location of the cardiac arrest, with higher survival rates in places where AEDs are more likely to be immediately available.
In addition, the use of an AED in conjunction with CPR (cardiopulmonary resuscitation) can further increase the chances of survival. According to the American Heart Association, the combination of CPR and AED use can increase the survival rate for cardiac arrest to as high as 45%. It’s important to note that these are averages from studies, and individual cases may vary. But in general, AEDs can play an important role in increasing the chances of survival for someone experiencing sudden cardiac arrest.
Clearly an AED is an invaluable tool to have during a cardiac arrest event, but AEDs can only save lives if they work properly in the moment they are needed. Imagine if the AED used by Damar Hamlin’s first responders had a dead battery, or was missing the pads, or was damaged. Damar might have had a drastically different outcome.
What are the Inspection Standards for AEDs?
OSHA standards do not specifically address AED usage and maintenance, but OSHA Publication 3185 (2003) encourages the installation of AEDs in workplaces and offers resources and guidance. There are also generally accepted inspection, testing, and maintenance guidelines that AED owners can follow to ensure that their devices are always ready for use.
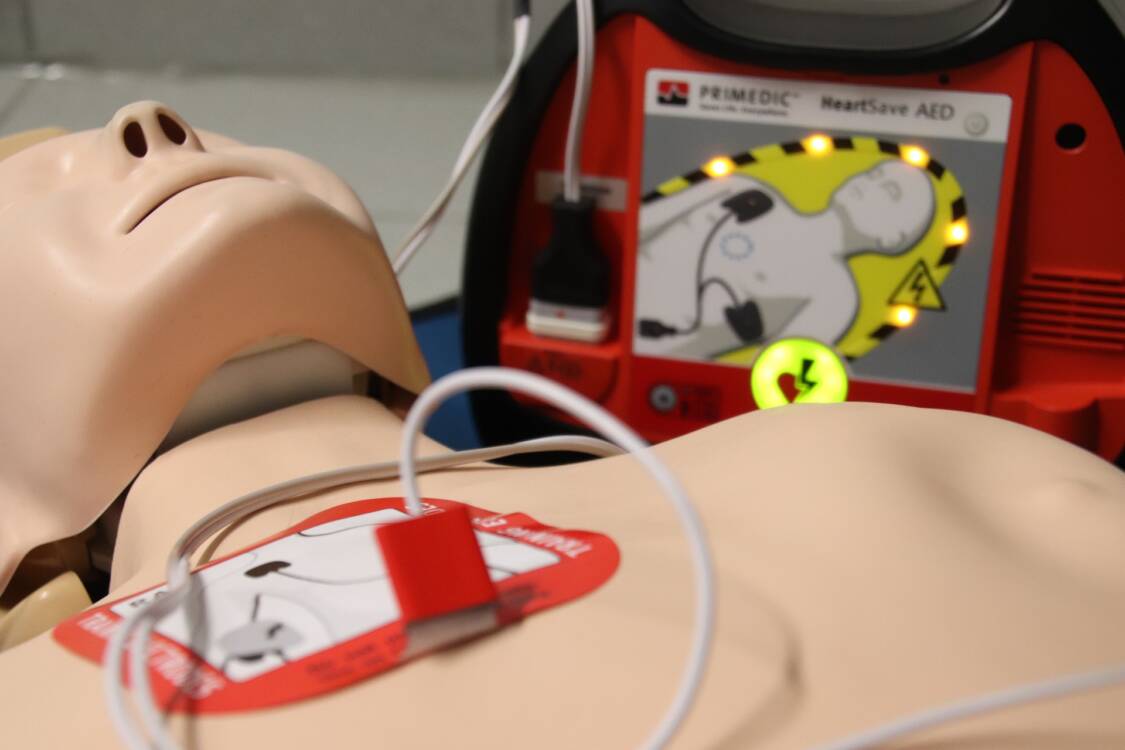
How Often Does an AED Need to be Inspected?
The frequency at which an AED needs to be inspected can vary depending on the manufacturer’s recommendations and local regulations. In general, it is recommended to inspect an AED at least once a month to ensure it is functioning properly and ready for use in case of an emergency.
It’s also important to keep the AED in a secure and accessible location. Also, it’s recommended to do an annual inspection by a qualified professional, which includes a more thorough check of the device including all the electrical and mechanical components.
How Do I Inspect an AED?
To inspect an AED (Automated External Defibrillator), follow these steps:
- Check the expiration date of the AED pads and battery. If either has expired, replace them.
- Turn on the AED and make sure it is functioning properly. Listen for a beep or check for a green indicator light.
- Check the AED pads for any damage, such as tears or discoloration. If the pads are damaged, replace them.
- Make sure the AED is clean and free of debris. Wipe it down with a damp cloth if necessary.
- Check the AED’s case or carrying bag to ensure it is in good condition and properly secured.
- Test the AED’s self-test function to make sure it is functioning properly.
- Record the date and result of the inspection.
Note that these are general inspection guidelines and it is important to follow the manufacturer’s instructions and recommendations for inspection and maintenance of the AED.
Are There Regulatory Standards for AEDs?
Yes, there are regulatory standards for AEDs. In the United States, AEDs are regulated by the Food and Drug Administration (FDA). The FDA classifies AEDs as Class III medical devices, which means they are subject to the most stringent level of regulatory oversight.
To be sold and used in the United States, AEDs must be cleared or approved by the FDA and must meet the standards set forth in the FDA’s Code of Federal Regulations (CFR) Title 21, Part 870.2250. These standards cover aspects of the device such as electrical safety, performance, labeling, and user instructions.
In addition to the federal regulations, some states have their own regulations for AEDs, such as registration and training requirements.
AEDs sold in Canada are regulated by Health Canada. They must be certified by Health Canada before they can be sold in Canada. Health Canada’s Medical Devices Bureau is responsible for reviewing the AEDs and ensuring that they meet the requirements of the Canadian Medical Devices Regulations.
The European Union also has regulatory standards for AEDs, which are regulated by the European Medicines Agency (EMA). AEDs sold in the EU must be CE marked, indicating that they comply with the requirements of the Medical Device Directive (93/42/EEC) and the Medical Devices Regulation (2017/745).
It’s important to note that these regulations are subject to change and updates, so it’s important to stay informed and comply with the latest requirements when purchasing and maintaining an AED.
How Can I Manage an AED Inspection Program?
Keeping track of each AED in your workplace and managing inspection and testing requirements can be challenging. It can be hard to remember where each device is located and when it was last inspected. Documenting and reporting on inspection dates and results can also be tedious. In general, the most effective way to successfully execute an AED inspection program is through the use of life safety inspection software such as InspectNTrack.
AED software, such as InspectNTrack, allows users to put a barcode on each AED to give it a unique identifier. It keeps an inventory of each AED including pertinent information such as its location, manufacturer, model number, and manufacturing date. The monthly inspection program is setup and managed by the software.
Each month InspectNTrack provides notification when AED inspections are due. It prompts users to scan the barcode on the AED. When the barcode is scanned, the user is required to answer each of the inspection questions which are similar to the ones described above. Inspection results are stored within the software, and inspection reports can be generated on-demand at any time. Compliance verification is only a button click away!
When an AED fails an inspection, InspectNTrack is setup with a customized workflow to ensure that the failure is corrected. Workflows can include sending out an email notification(s), creation of a work order within your work order management system, logging the issue in InspectNTrack’s discrepancy module, or creation of consolidated failure reports. The workflows are built with the ultimate goal in mind of finding AED issues and correcting them as quickly as possible.
Conclusion
Automated external defibrillator (AED) devices, are powerful life saving tools. In order to keep them functioning properly, it is imperative that regular inspections and maintenance be conducted on them. To learn about the established standards for AED upkeep, review OSHA publication 3185 and the FDA regulations. Maintaining a reliable inspection schedule can be a difficult task; however, technology solutions, such as InspectNTrack, are here to simplify it. Learn more about INT’s inspection software and safety solutions by requesting a demo!